Generative Design & The Role of AI Engineering - Applied Use Cases
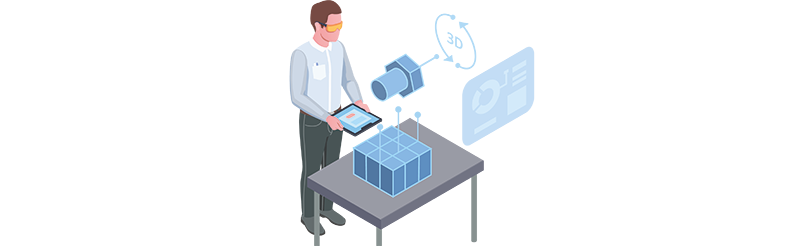
Let's discuss generative design in the context of artificial intelligence (AI) engineering.
Developing design solutions generated automatically (with input factors) is not new. In 2023, a range of full-fledged solutions for AI-driven simulation makes generative design very appealing.
But first, why would one want to consider generative design instead of established methods?
One of the most evident is the possibility of generating complex geometries with generative design. Generative design can create complex geometries that may not be possible with traditional manufacturing methods, such as internal structures and lattice patterns, which can help improve the final product's performance and functionality.
Another advantage is the high degree of customization. Generative design can be used to create customized products, as the design can be easily modified to meet the customer's specific needs. This can increase the appeal of the final product.
Moreover, we will see that by coupling design and simulation, generative design can optimize a design for specific performance criteria - such as strength, weight, and cost - leading to improved final product performance. Engineers can utilize generative design to optimize existing designs to reduce weight, increase performance, or lower production costs, thus giving their companies a competitive edge.
Therefore, generative design has the potential to revolutionize the way we design products and manufacture them because it enables designers and engineers to explore a much more extensive range of design options and find optimal solutions.
What Is the Generative Design Software Workflow?
Generative design allows designers and engineers to explore a much larger design space than a human operator.
A designer or engineer will decide the design's restrictions and goals before beginning the generative design process.
The generative design process is iterative.
The steps (see figure below) are repeated as needed in an iterative design process until an optimal design is found.
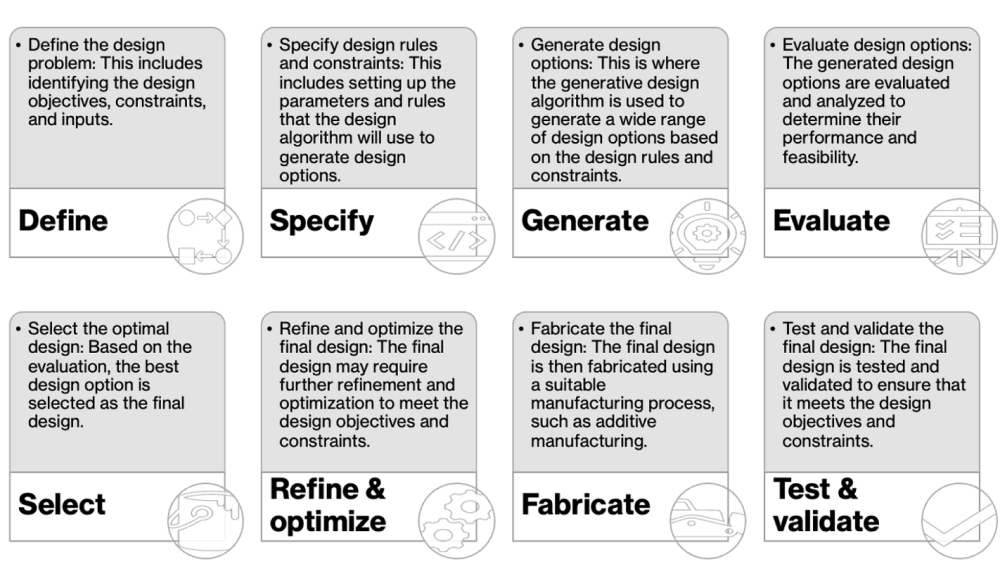
The generative design process can be carried out "by hand" or through software that automates the process. Generative design technology can use different algorithms; such as evolutionary algorithms, swarm intelligence algorithms, or artificial neural networks, to generate design options.
Design engineers can then examine the various options and choose the ones with the most potential, after which they can modify and improve them.
The figure shows a typical process independent of the generative design software used.
Traditional Subtractive Manufacturing Processes - an Overview
A traditional subtractive manufacturing method is a process in which material is removed from a solid block, also known as a billet, to create a final product.
This is in contrast to additive manufacturing, or 3D printing, in which material is added layer by layer to make a final product.
The below methods are considered traditional since they have been used for many decades or even centuries and are well-established. They are widely used in manufacturing to create a wide range of products, including precision parts for aerospace, automotive, and consumer goods.
In CNC machining, we use a cutting tool (such as a drill or mill) to remove material from a metal or plastic block.
A lathe is a machine tool used for turning, drilling, and cutting by rotating the workpiece on its axis.
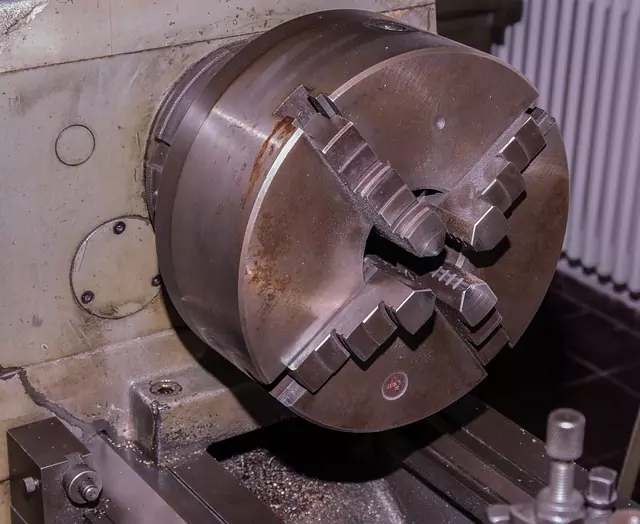
With grinding, an abrasive wheel removes material from a workpiece.
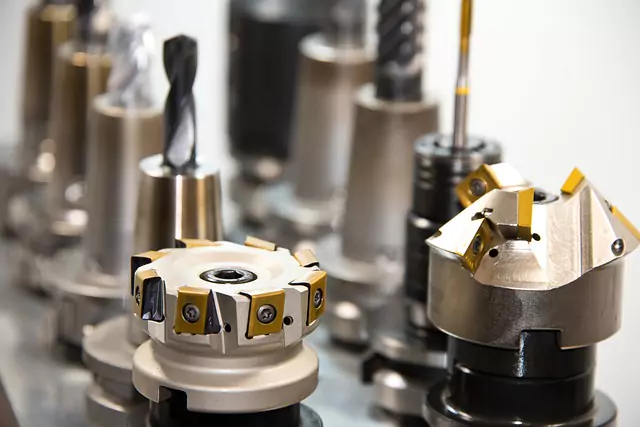
With milling, a rotating cutting tool removes material from a workpiece.
What Are the Most Advanced Manufacturing Processes in 2023?
In the past few years, 3D printing has become increasingly popular. 3D printing (a.k.a. additive manufacturing) is considered one of the most advanced manufacturing processes because it creates complex geometries and designs that are difficult or impossible to produce with traditional manufacturing methods.
3D printing allows for creating of products with intricate internal structures, such as hollow spaces and lattice patterns, which can help reduce weight and improve performance.
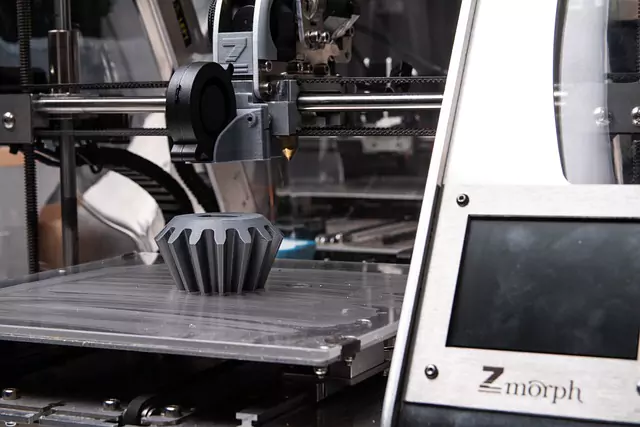
In addition, 3D printing allows for on-demand production. On-demand production means that products can be created as needed without needing large-scale production runs. This can help to reduce waste and improve efficiency.
Another advantage of 3D printing is the ability to use a wide range of materials, including metals, plastics, ceramics, and even biological materials, which allows for creating products with unique properties and improved performance.
Finally, 3D printing allows customized products, as the design can be easily modified to meet the customer's specific needs. This has led to the developing of new business models, such as on-demand manufacturing and mass customization, driving innovation in many industries.
The below figure summarizes a few of the generative design advantages.
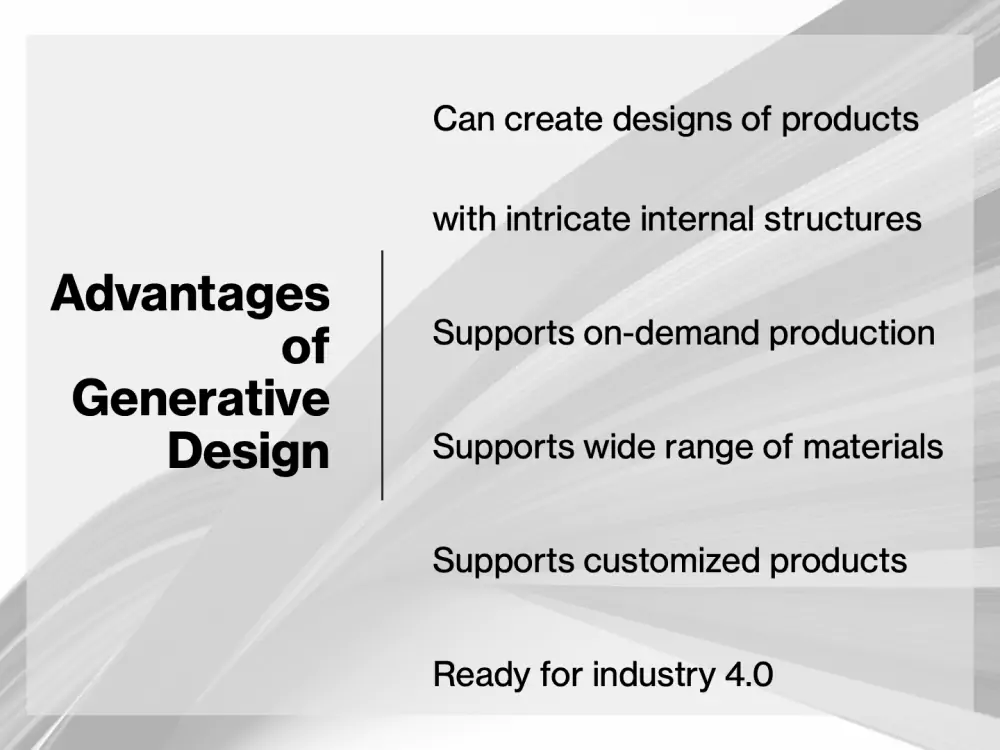
What Is the Relationship Between Additive Manufacturing Methods for 3D Printing and Generative Design?
We could summarize by saying that additive manufacturing / 3D printing and generative design "help each other". How so?
Generative Design Supporting Additive Manufacturing Methods
Generative design is frequently used to optimize designs for additive manufacturing. Therefore, there is a close connection between the two processes. Generative design software creates various design iterations in response to user input of parameters and constraints.
After considering these alternatives, the best design for a given manufacturing process can be determined. This has the potential to increase production output while simultaneously decreasing material waste.
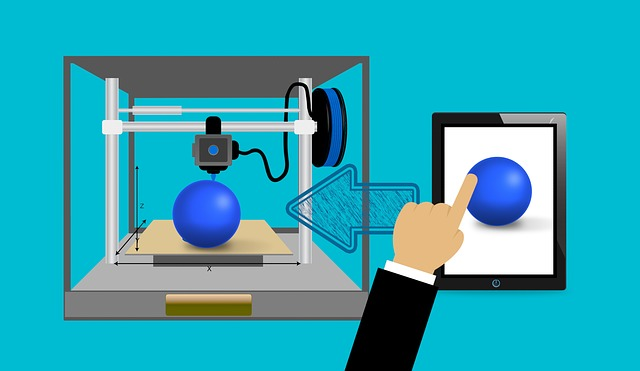
Additive Manufacturing Methods Supporting Generative Design
The complex geometries created with additive manufacturing make it an ideal fit for generatively designed products that cannot be produced using more conventional methods. Additive manufacturing and generative design work together to speed up and improve the product development process.
Caveats of Generative Design
There are several usual caveats to consider when using generative design. The following use cases will show how AI-driven optimization algorithms and AI-driven simulation overcome most of those caveats.
Generative Design and Manual Intervention
While generative design can facilitate the automation of the design process and the exploration of more design choices, more is needed for human scrutiny. The program may create design solutions, but engineers and designers must still study and evaluate them to ensure they are feasible and adequate.
Generative Design Feasibility
Implementing a generative design technology can be challenging, often requiring niche programs and knowledgeable personnel. Software use requires engineers and designers to be conversant with generative design principles and the application of AI algorithms.
Generative Design Limited Design Space
While generative design aids in exploring a wider variety of design choices than would otherwise be available, the engineer's or designer's input parameters and limitations still constrain the scope of this exploration.
Generative Design Budget
Implementing a generative design process can be prohibitive for some businesses, as generative design software and associated costs can be challenging.
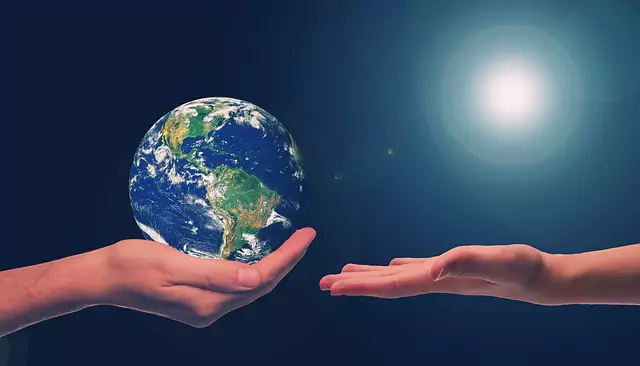
Generative Design Ethics
The use of generative design may raise legal and ethical concerns, such as who owns the rights to the designs created using the method and the possibility of discriminatory or prejudiced outcomes.
Engineers and designers should be aware of these concerns and consider them during the design process.
Generative Design Algorithms
Generative design algorithms are a type of computer software that uses mathematical algorithms to generate a wide range of design options based on input parameters and constraints. These algorithms can optimize a design for a specific manufacturing process, material, or performance criteria.
There are several types of algorithms for generative design, including artificial neural networks. AI algorithms are inspired by the structure and function of the human brain and use techniques such as deep learning applied to engineering to generate new design options.
Machine Learning, Deep Learning, and Generative Design
Introduction to Machine Learning
Machine learning (ML) is a technique for teaching a computer to perform a task without being explicitly taught how to accomplish that work by a human.
How does the machine learn?
A computer is given a set of data and a set of rules, and it uses those rules to learn from the data, and then it can make predictions or decisions based on that learning.
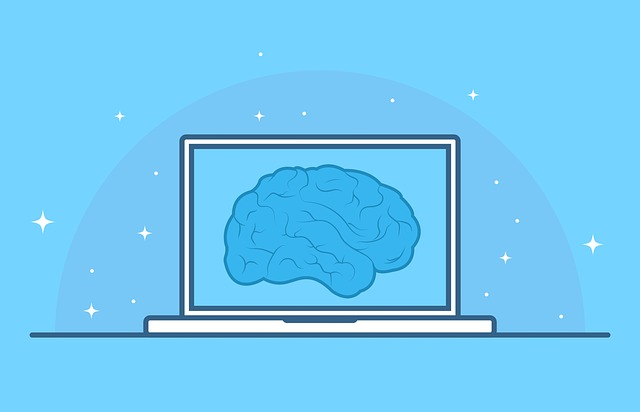
Examples of ML applications include self-driving cars, speech recognition, and image recognition. ML is used in various industries and applications, from healthcare to finance, security, and customer service.
From Machine Learning to Deep Learning
Deep learning is a subset of ML that use artificial neural networks with layers over layers of artificial neurons to process and evaluate massive volumes of data. It is particularly successful in image recognition.
An artificial neural network is a mathematical structure (easily transferrable into pieces of software) modelled after the human brain is designed to recognize patterns. It works by processing input data through layers of interconnected nodes or neurons; each layer building on the previous one to extract more complex features from the data. The more layers a neural network has, the deeper it is, hence the name Deep Learning.
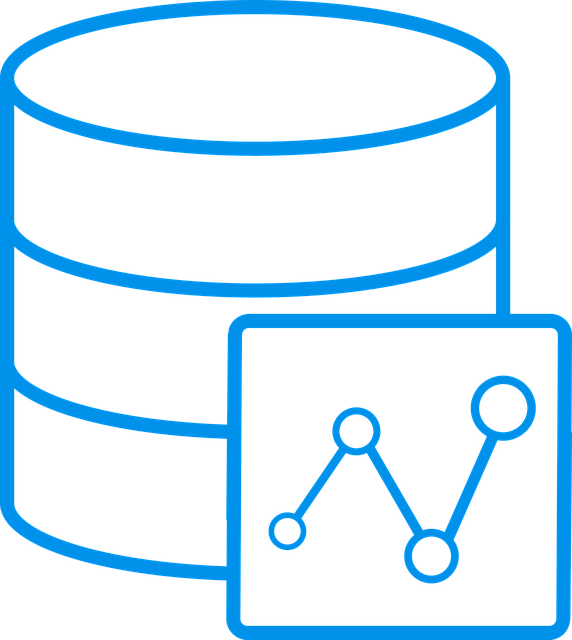
Non Mathematical Proof that Deep Learning Learns
A typical deep learning model has an input layer, multiple hidden layers, and an output layer. The hidden layers comprise many neurons connected by weights and biases. The weights and biases are changed through optimisation to learn the model's parameters that are ideal for giving an accurate response (i.e. a prediction).
Backpropagation is the most common optimization algorithm used to train a deep learning model.
Backpropagation is based on an algorithm called gradient descent that adjusts the weights and biases of the model until a so-called cost function.
The cost function measures the difference between the model's predictions and the true values and measures the model's performance.
Hence, without any mathematics, we have shown that deep learning can learn to acquire predictive capabilities!
From Deep Learning to Real-Time Simulation
Computer-aided design (CAD) is being revolutionized by integrating artificial intelligence algorithms. These algorithms can accelerate the design timeline by exploring various design alternatives and possibilities. This allows for the rapid generation of new design ideas and for identifying the most optimal design solutions. Integrating AI (as a surrogate of CAE simulation) into CAD software, either embedded in the CAD software or as geometry import capability, provides an integrated solution that streamlines the product design process.
How can deep learning provide a surrogate or emulator for CAE? Deep learning models can use data from experiments, CFD simulations, or other sources to make predictions about fluid flow behaviour without solving the underlying equations of fluid dynamics.
Concerning the status of deep learning, its models can approximate the behaviour of complex physical systems, such as fluid dynamics (CFD), without the need to solve the underlying equations.
Pre-trained models are starting to become available. They can be fine-tuned to specific applications, allowing predictions to be made quickly without requiring extensive training.
It is important to note that deep learning may not replace CFD in all cases, as it can be dependent on the quality and quantity of the data it was trained on. Deep learning models may not be accurate in cases where the physics of the system is poorly understood. The well-known "garbage in, garbage out" principle is always valid!
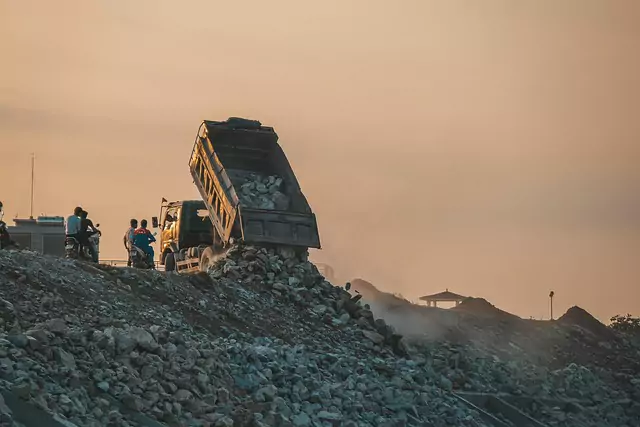
Generative design tools that could rely on a real-time CFD solution would show the clear advantage of working on the simultaneous exploration of new shapes and their simulation. Thus, the design exploration process can solve complex challenges and enable an accelerated design timeline, something unthinkable with traditional processes.
Cases of Generative Design Solution Supported by AI Prediction
Aerospace Industry Example 1 - Aircraft Wing
Generative Design can be beneficial for optimizing the design of a wing, as it can help to reduce weight while maintaining or improving performance. Generative design can help engineers find new and innovative ways to design lighter, stronger, and more efficient wings, thus having a cost-effective final product.
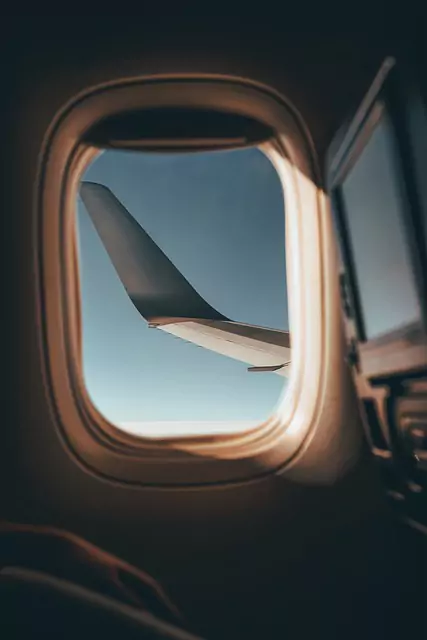
Aerospace Industry Example 2 - UAV Shape
There are several design challenges affecting the design of Unmanned Aerial Vehicles (UAVs). UAVs have a limited payload capacity, and a large portion must be dedicated to the power source (e.g. a battery). This means that the weight of the aerodynamic design must be kept to a minimum to maximize the weight available for the power source. Therefore, the design goals include lightweight parts while envisaging manufacturable designs.
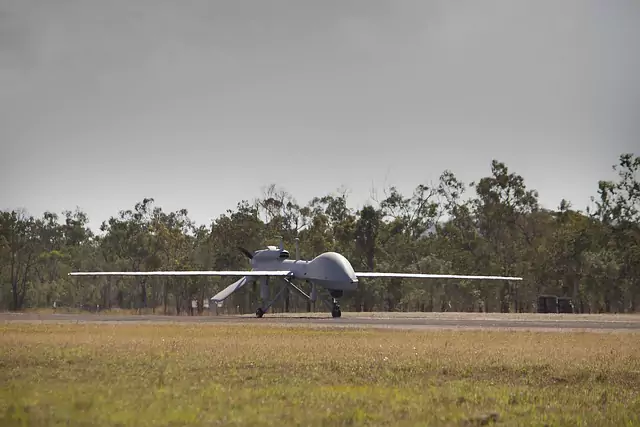
Generative design can be used to help design an UAV with aerodynamic optimization. Generative design algorithms can explore a wide range of options and find the most aerodynamically efficient shape for a UAV. This can help reduce drag and increase the overall autonomy of the vehicle. A use case shows the aerodynamic optimization of a UAV in terms of increasing its Lift to Drag ratio.
Aerospace and Defense - Summary and Way Forward
Neural Concept is very active in the field of artificial intelligence in aerospace.
Neural Concept and a leading aerospace company extended collaboration with the common objective to keep pushing the deployment of new design methodologies in aerospace based on deep learning. The partnership aims at making the power of deep learning accessible to design engineers for real-time simulation and interactive design optimization. This will help accelerate and improve the engineering of next-generation aircrafts and remain leaders in the industry.
Automotive Example 1 – Car Spoiler
Car spoilers are aerodynamic devices that disrupt the airflow over a vehicle, reducing lift and increasing drag. Optimizing the design of a car spoiler can help improve a vehicle's aerodynamic performance, which can be important for applications such as racing or high-speed driving.
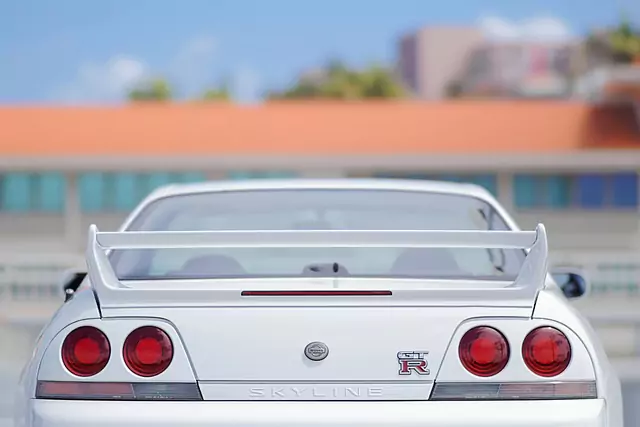
Automotive Example 2 – Car Rear Mirror
Optimizing the design of a car's rearview mirror can help improve the vehicle's performance and efficiency. For example, a lighter and more aerodynamic mirror design could reduce drag and improve fuel efficiency.
Using generative design to optimize an automotive component, such as a side rearview mirror, engineers can help improve the vehicle's performance and efficiency.
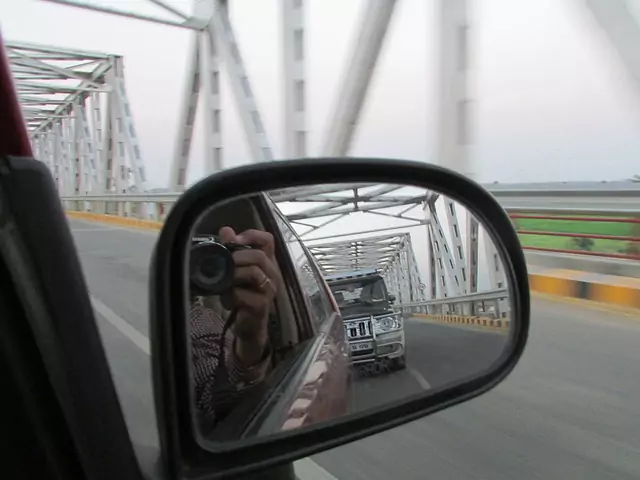
Automotive Industry - Summary and Way Forward
Neural Concept is very active in artificial intelligence in the automotive industry, with solutions supplementary to traditional CAE tools.
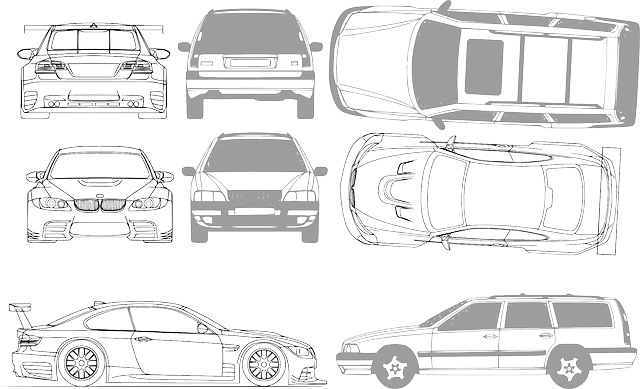
The advantage of deep learning is a tremendous acceleration of optimization design loops, thus making it possible to have a faster generative design with more constraints and therefore making it possible to solve forbidding engineering challenges within hours instead of weeks, such as simultaneous exploration of the design solutions, the satisfaction of performance indicators and finally satisfying manufacturing processes.
Several use cases of AI-driven optimization and simulation show that 2023 is the maturity year for AI technology.
Thus, ideally, AI would shape a CAD model describing a design achieving the targeted weight reduction that would simultaneously meet constraints on manufacturing costs, satisfy mechanical requirements checked with 3D simulation and thus show the full benefits of generative design by being a truly optimized design.
Several use cases, for example, a case of optimization of heat exchangers that led to optimal innovative geometries, show the benefit of coupling AI-driven shape modification and simultaneous simulation.

Similar Methods: Topology Optimization
Generative design and topology optimization are both computational methods used to optimize a product's design. Topology optimization (TO) is called so because it is a method that optimizes the topology of a design, which refers to the shape, layout and distribution of the material in a design. Both TO and generative design can generate multiple design options based on input parameters and constraints and then evaluate them to find the optimal solution.
Some similarities between generative design and topology optimization are:
- Both use optimization algorithms to generate a wide range of design options based on input parameters and constraints.
- Both optimize the design for specific performance criteria, such as strength, weight, and cost.
- Both can create complex geometries that may not be possible with conventional manufacturing technologies.
- Both can be used to optimize designs for additive manufacturing.
- Both can be used to optimize designs for multi-objectives (e.g. strength and weight, cost and performance)
- Both can reduce material usage and increase the final product's performance.
Differences Between Topology Optimization and Generative Design
What are the main differences between topology optimization and generative design?
TO finds the optimal layout of material in a design. It is mainly used to optimize the distribution of the material in the design and reduce material usage while maintaining or improving the final product's performance. Topology optimization is more specific than generative design and is mainly used for structural design optimization, although there are different application examples, such as in fluid dynamics.
Conclusions - Advantages of Generative Design
To summarize, generative design can generate various design options based on inputs such as geometrical shapes and constraints.
We have shown what the three best combinations for generative design are:
- Additive Manufacturing
- CAE Simulation
- AI-Driven Simulation and Optimization
In combination with additive manufacturing, generative design enables a more efficient and effective product development process by allowing for the exploration of various design options, the production of complex geometries and lightweight structures, and rapid prototyping and testing.
In combination with CAE simulation, generative design makes it possible to find an optimized design that meets the desired performance goals by simulating a physical test well before it takes place (or replacing it).
The ultimate combination is AI-driven simulation and optimization. Taking the previous concepts further: when CAE simulation can be surrogated or "complemented" by real-time AI (deep learning) prediction, optimizing performance can become a matter of real-time operation. In fact, by delivering results several orders of magnitude faster than CAE, deep learning prediction accelerates the time-consuming CAE software to speed up design cycles.
Moreover, optimization algorithms work in conjunction with AI, thus creating a fast AI equivalent to the time-consuming optimization campaigns of CAE and traditional optimization software.