Mastering Automotive Product Development: Key Strategies for Success
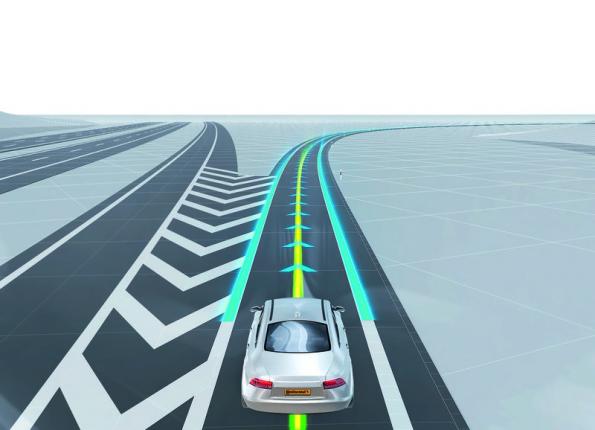
Product development in the automotive industry has evolved from decade-long cycles to rapid, data-driven iterations. In the 1980s, bringing a new vehicle to market required 5–7 years. Today, intense competition and shifting consumer demands have compressed that timeframe to just 2–3 years.
With this acceleration, traditional development methods—reliant on physical prototyping and sequential design iterations - are reaching their limits. Can AI push the boundaries further?
The article explores how Artificial Intelligence modernizes all phases of vehicle development in the increasingly competitive automotive industry. AI streamlines processes, reduces TTM with accelerated design, and drives innovation by helping engineers explore the design space with more scope.
In the article, we give details on the advanced technologies shaping product development within the sector.
Automotive Product Development Phases and Tiers
Automotive product design follows a structured workflow from concept to market launch. The industry starts with concept development, outlining features, and marketplace positioning. Before the final release, all tiers collaborate to design a vehicle meeting climate change and safety regulations to avoid recall campaigns undermining their cost-reduction efforts.
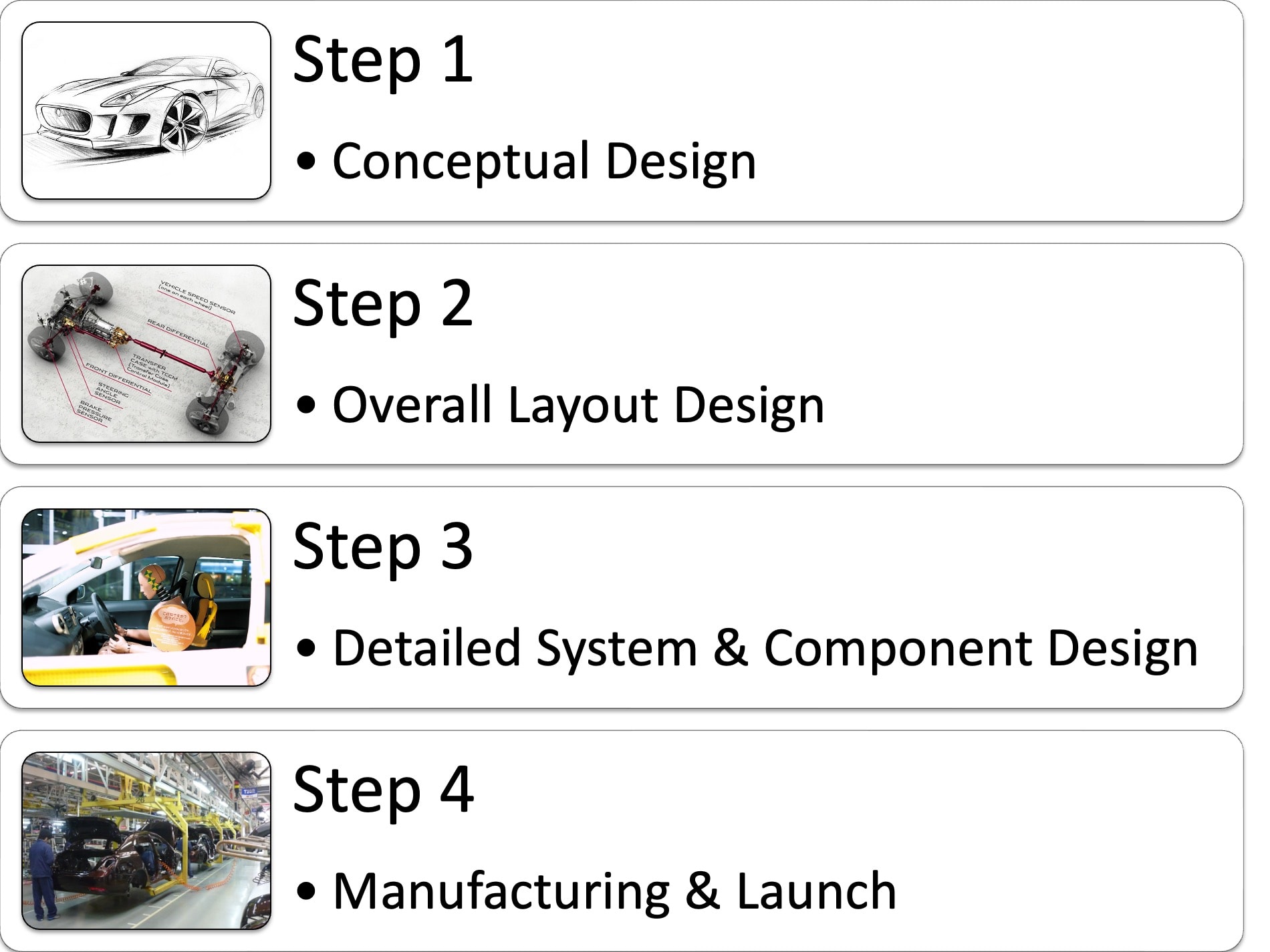
Phases in Product Development
Below, we will show the order of Conceptualization, Overall Layout Design, Detailed Design, and Manufacturing to organize the product development process and determine the specific engineering resources for each phase.
1. Conceptualization
Conceptual design, which involves sketches and early models, defines the vehicle’s form and purpose. Designers use CAID (computer-aided industrial design) for aesthetics, ergonomics, and initial surface modeling before detailed engineering.
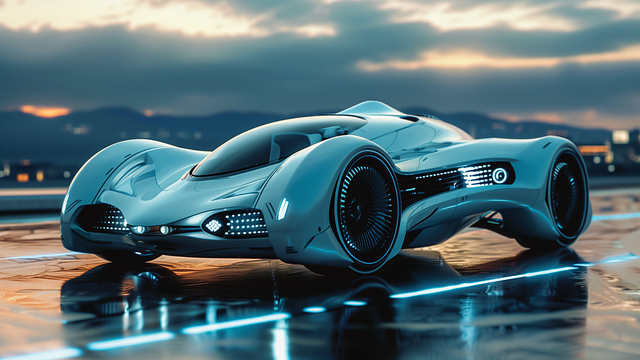
2. Overall Layout Design
Designers use CAD for components and assemblies in the design and engineering stage.
Simulation improves product performance, manufacturability, vehicle safety, and functionality. In fact, with simulations, automotive professionals can assess a vehicle’s crashworthiness (how energy is absorbed by the structure and occupant safety in crash scenarios) and noise, vibration, and harshness performance (to improve comfort and durability and reduce unwanted noise for drivers and passengers).
Parts of assemblies of cars (often delegated by OEMS to suppliers for the full "ingegnerizzazione" and manufacturing) can be of any nature:
- aerodynamic parts: diffusers, spoilers, underbody panels...
- turbo machinery such as turbochargers, superchargers, e-boosters..
- electronics, such as ECUs, sensors, wiring harnesses, ADAS modules...
This also depends on whether the powertrain is internal combustion/hybrid or fully electrical (combustion engines, electric motors, hybrid drivetrains, inverters, battery packs, etc.). The number of parts can reach a staggering 30,000 and may be reduced to "only" 10,000-20,000 for electrical/hybrid vehicles!
On top of performance concerns, every product in the automotive industry should meet regulations criteria. Regulations are addressed during the overall layout and detailed design phases. Engineers ensure compliance with vehicle safety, emissions, and performance standards via simulation, laboratory, and track testing to evaluate vehicle dynamics and emissions.
3. Detailed System / Component Design
Detailed design refines structures, ensuring performance and manufacturability. Prototyping and testing are encountered here. Until the '90s, laboratory or track testing was the only way to validate a product before mass production. The prototype undergoes several tests and evaluations to ensure it can perform well; thus, testing, including crash tests and durability, was the only way to assess performance and safety before production. From the '90s to the mid-20s, simulation often replaced experiments because of its cost-effectiveness, speed, and depth of insight.
However, even simulation wait times can impact time to market! Heavy HPC (high-performance computing) investment helps respect project schedules. The complexity of simulating real-world scenarios is also a challenge for automotive design and simulation.
Before tackling AI, let us review how the automotive industry is structured.
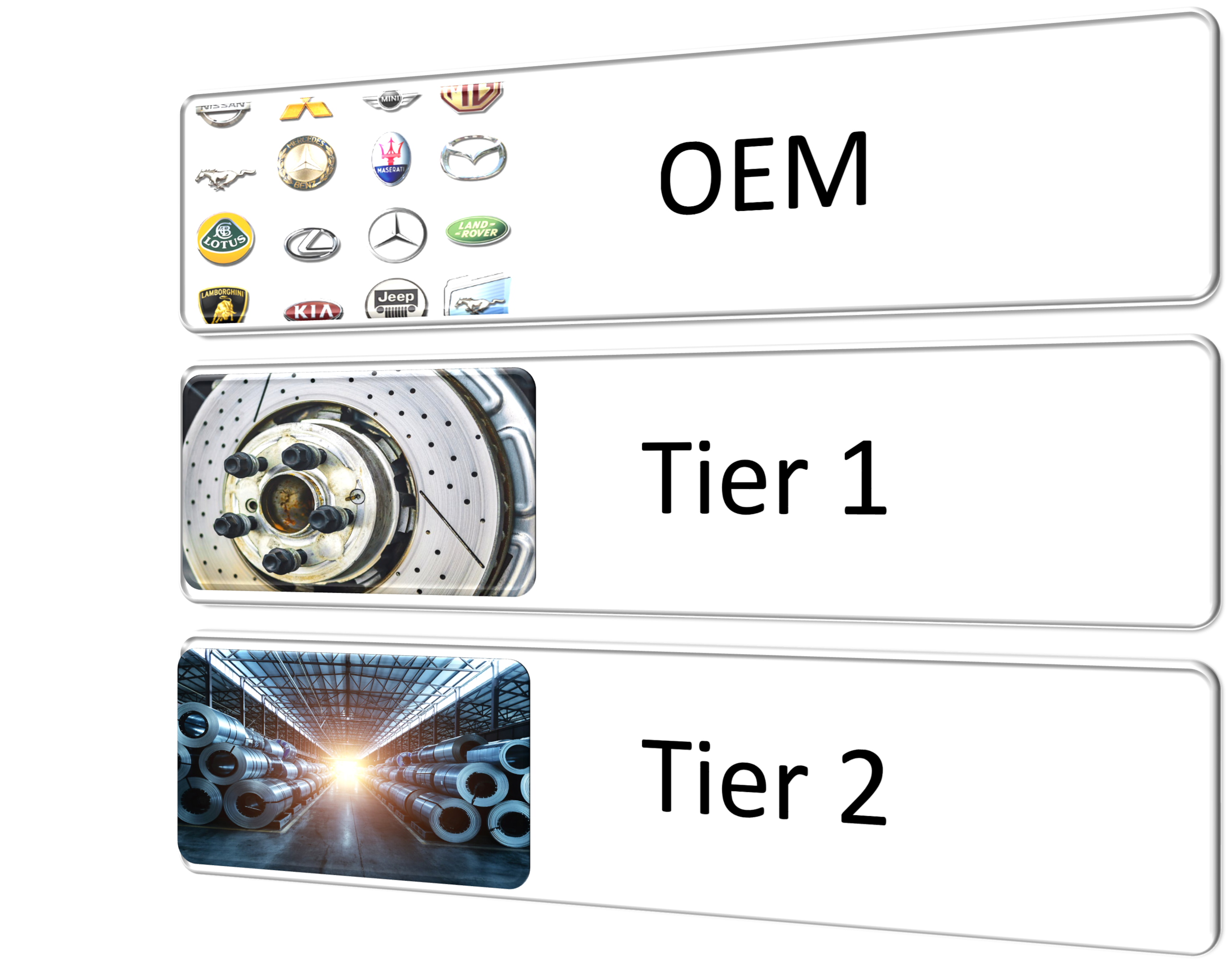
Three Levels in the Supply Chain Hierarchy
The supply chain is structured into tiers with roles and responsibilities in engineering product development. Failure is not an option here. For example, delays from a critical Tier 2 supplier will delay Tier 1 and OEMs. Supply chain management in the automotive industry serves to avoid such disruptions.
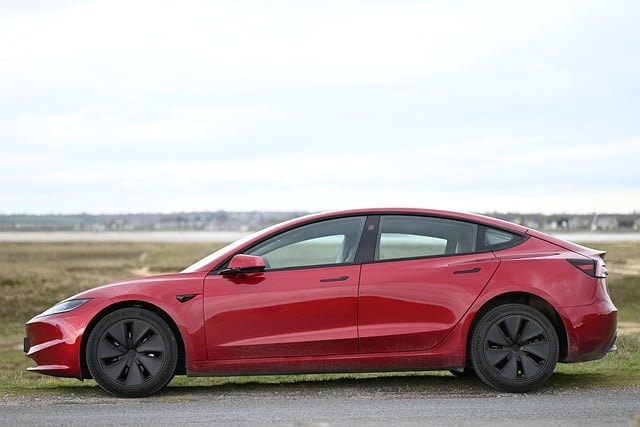
OEMs
Original Equipment Manufacturers (OEMs) assemble vehicles under their brand names. They have advanced technologies and rely on suppliers for specialized innovations, like next-generation battery systems. OEMs define software standards to ensure collaboration across the supply chain. The product lifecycle requires engineering expertise, efficient development processes, and the creation of modular platforms. Product life cycle management (PLM) facilitates coordination between manufacturers by implementing workflows involving project management, quality, simulation, research and innovation, engineering, etc.
Many factors influence OEM strategies, including raw material costs and supply chain disruptions. Target market dynamics push OEMs to adapt to market trends. Emerging technologies introduce new challenges, and OEMs must integrate AI and sensor fusion systems. Advancements in automated driving require validation and cybersecurity measures.
Also, shifts in regulatory standards and market trends toward electrified vehicles force OEMs to innovate vehicle development.
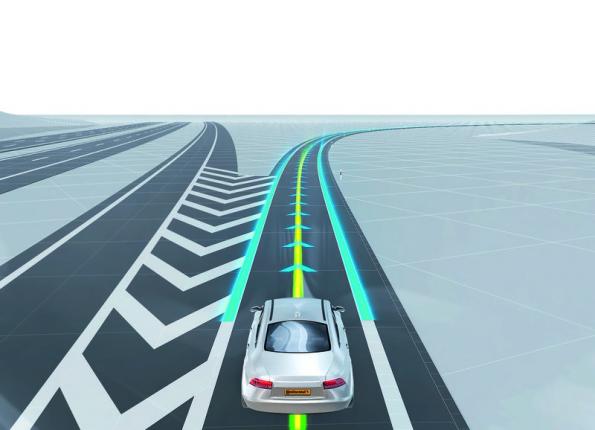
Tier 1 Automotive Companies
Tier 1 automotive companies provide OEMs with systems or assemblies essential to vehicles. They design, engineer, and manufacture to meet quality standards. Examples include Bosch for electronics systems and Denso for HVAC. These companies exhibit technical knowledge and innovation.
Tier 2 Automotive Companies
Tier 2 companies provide parts or materials to Tier 1, often focusing on specific components or raw materials. For example, a steel manufacturer supplying metal to a Tier 1 company would be considered a Tier 2.
AI and Automotive Product Development
Addressing the following challenges is crucial for the collaboration between OEMs and Tier 1 suppliers, which aims to enhance efficiency, reduce costs, and accelerate TTM. Prototyping and testing times can delay market entry, limiting prototype production and affecting the depth of refinement.
Simulations have evolved beyond testing, offering quicker, more cost-effective iterations and deeper analytical insights. However, this is insufficient since even the fastest simulation cannot occur in seconds. This is reflected in its name, "analysis," which always follows design changes. How can designers instead benefit from real-time suggestions?
Two Artificial Intelligence (AI) branches come to help here.
Machine Learning (ML) enables systems to learn from data without explicit programming. Deep Learning (DL), a subset of ML, uses computer vision techniques and neural networks to analyze 3D patterns and predict engineering outcomes. These AI technologies improve TTM in automotive product development, as shown below. Some software specializes in one phase (CAS for concepts, MES for the manufacturing process), while AI can help throughout product development.
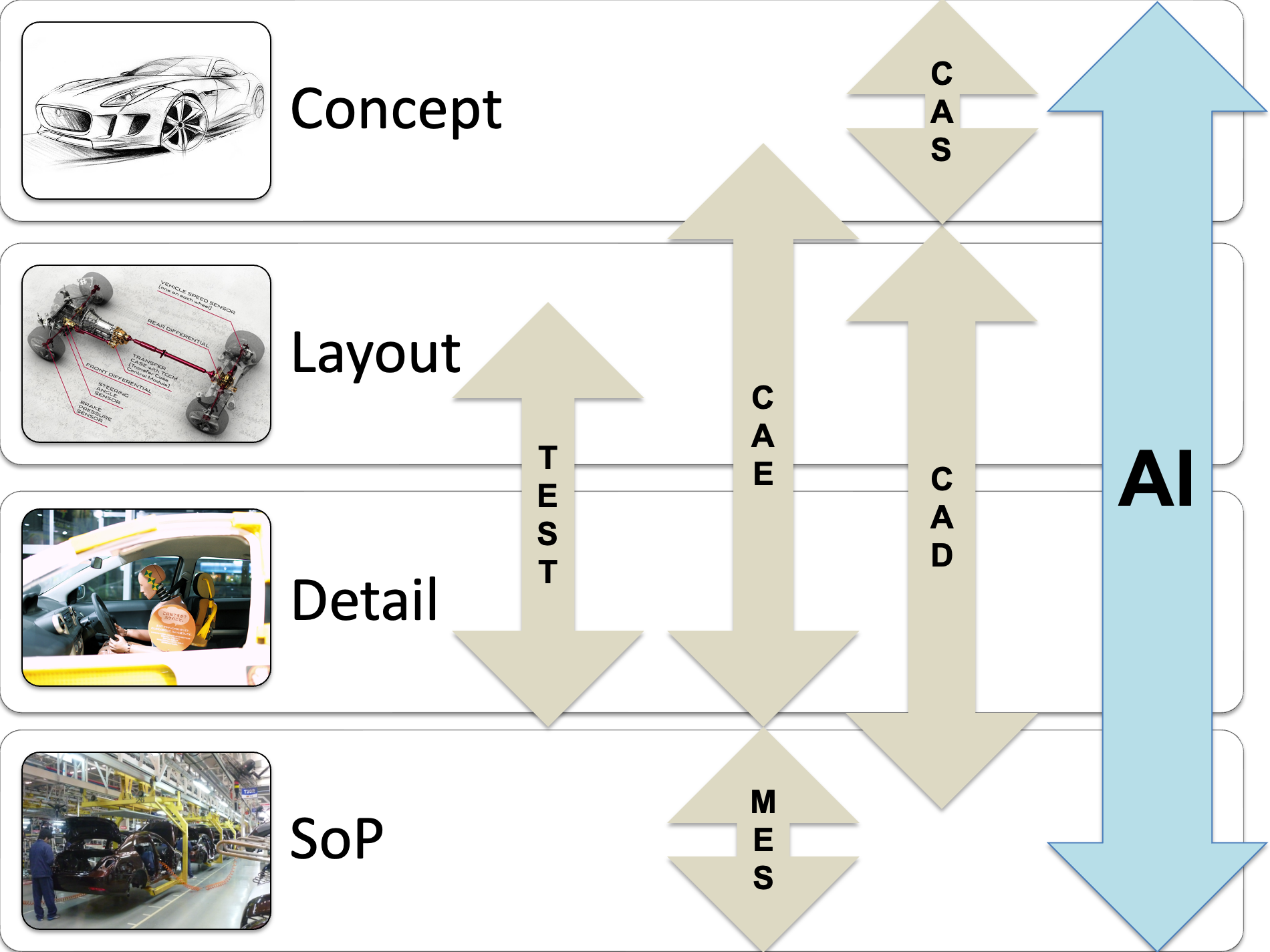
Design Iterations
Through CAE simulation tools, teams evaluate a vehicle’s crashworthiness, structural integrity, and material durability. AI surrogates use data from CAD and simulations to develop predictive models that explore a broader and deeper design space.
As the automotive industry is phasing out internal combustion engines in favor of cleaner electric vehicles to reduce emissions, automotive companies are using simulations to evaluate the effects of alternative fuels, lightweight materials, and energy-efficient technologies. Balancing the development of electric vehicles and internal combustion engine vehicles is a challenge for automotive manufacturers.
As we will see in the success stories later:
- AI tools optimize vehicle components based on performance indicators like aerodynamic efficiency. Models trained on simulations for aerodynamics help computationally expensive simulations.
- AI models help crash simulation data without prototype builds.
Thus, simulations before physical testing yield several benefits:
- Accelerated development timelines: advanced technologies in AI accelerate iterations in simulations, reducing TTM for new vehicle models.
- Reduced errors: Machine learning enhances predictive analytics, minimizing design flaws earlier in development.
Costs Associated with Physical Prototyping
AI-driven simulations cut materials, labor, and testing costs. Thus, manufacturers achieve efficient development cycles and better quality and adapt to market demands with AI-powered product development automation.
Data Management
AI product development enhances data management by automating critical vehicle data collection, design specifications, and performance metrics. With AI, manufacturers can streamline compliance with safety and environmental regulations, reducing errors and improving efficiency.
Industry Examples
We will show how leading automotive companies have successfully integrated AI technologies into their development processes with benefits in product quality with business cases. Continuous simulation and testing data generation during the project phase reduce the dataset investment. In the future, the full complexity of components and assemblies will be within the reach of any designer implementing AI-driven workflows and decision-making processes. This leads to a future with accelerated innovation and better usage of resources.
F1 Aerodynamics
Motorsport helps the auto industry develop cutting-edge technologies. Like space missions or the America’s Cup in sailing, F1 Aerodynamics pushes the boundaries of engineering, with innovations trickling down to standard passenger vehicles.
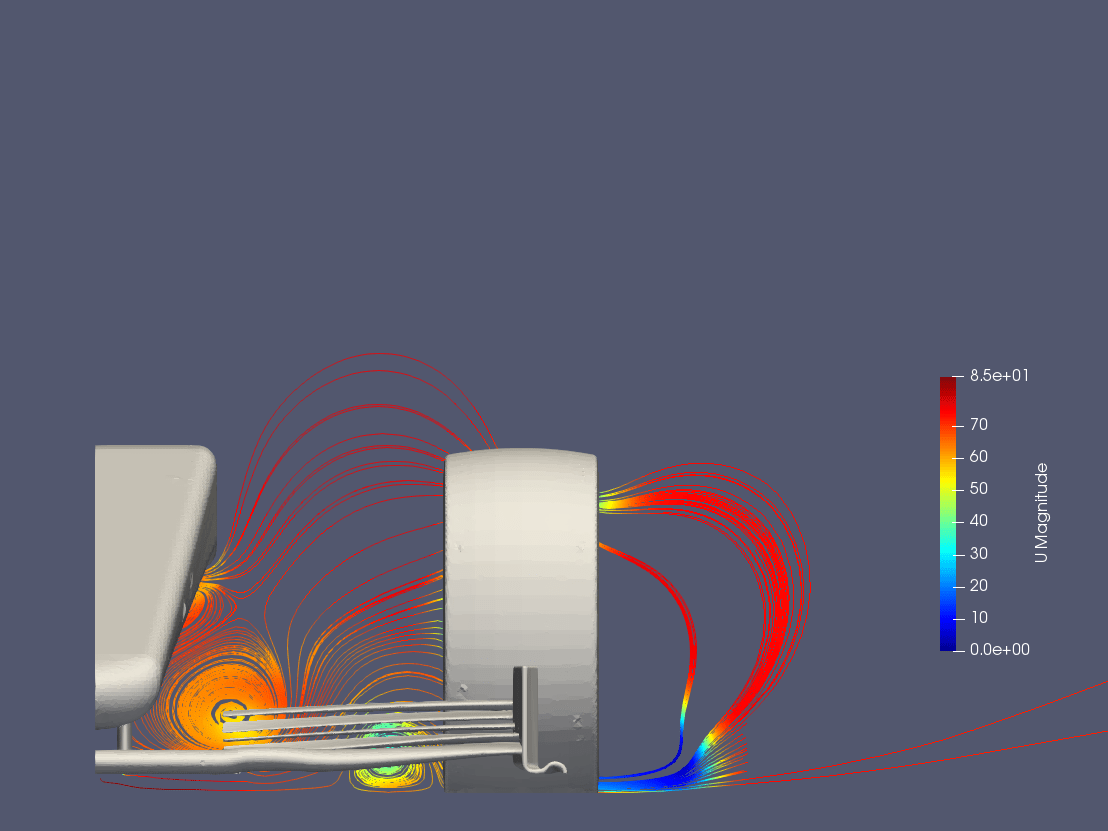
Subaru Success Story
Subaru introduced a revolution in automotive development with the Neural Concept platform, which helped capture 3D shape features. This led to faster and more accurate predictions of the forming process. Engineers reduced die face shape design analysis times from 3 hours to 2 minutes, with accuracy and quality comparable to engineering simulation.
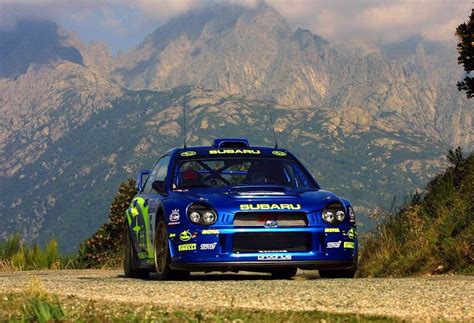
Mubea Success Story
At Mubea, Deep Learning networks learned to predict battery contact during crash events. Thus, designers could get feedback on innovative lightweight solutions without waiting for traditional simulation. The figure compares deformations from simulation and AI.
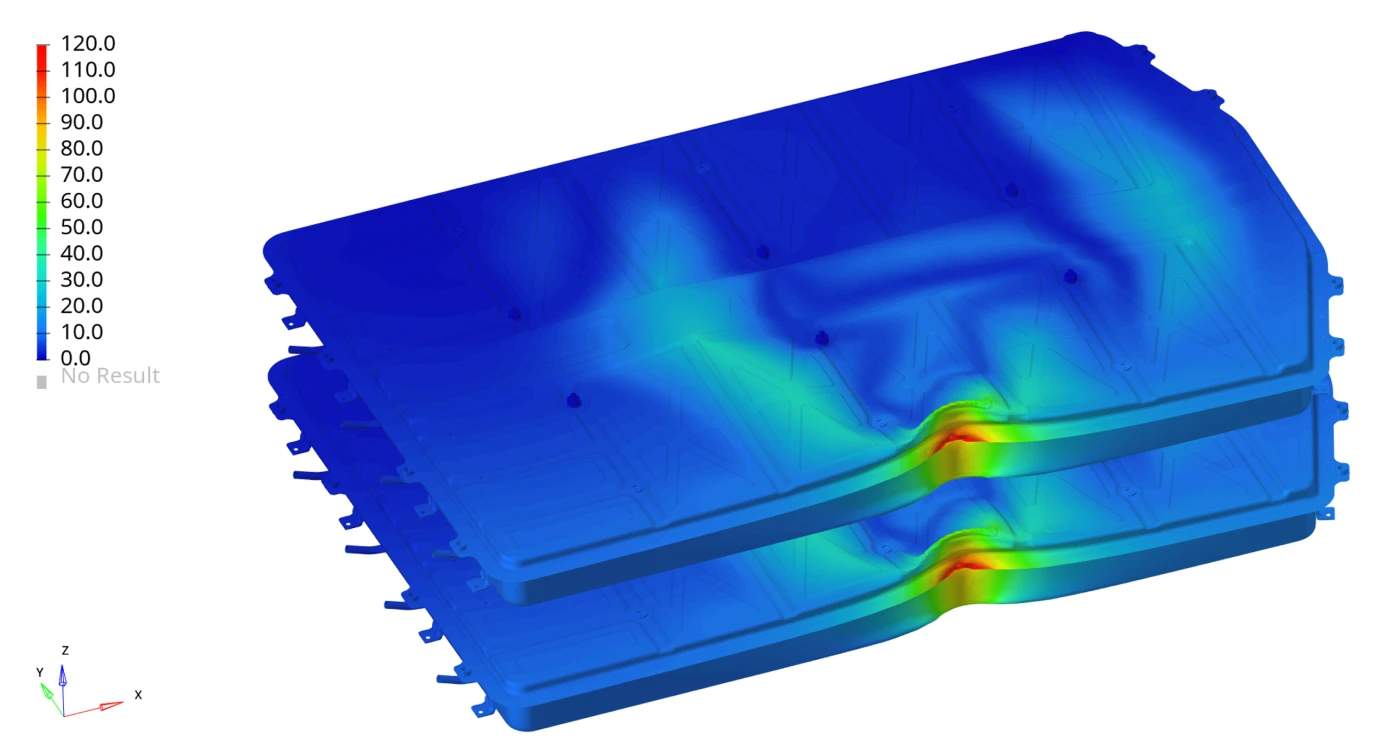
Eaton Success Story
Eaton Innovation Center leveraged datasets developed with its engineering expertise in cold plate design. Using technologies from Neural Concept, Eaton accelerated their design life cycle by utilizing previous knowledge and data. This workflow improved pressure drop by 30%+ and reduced weight by 10%+ in cooling modules, better than conventional CAD-CAE. A technical paper about this success story of Deep Learning application to a thermal management device is downloadable.
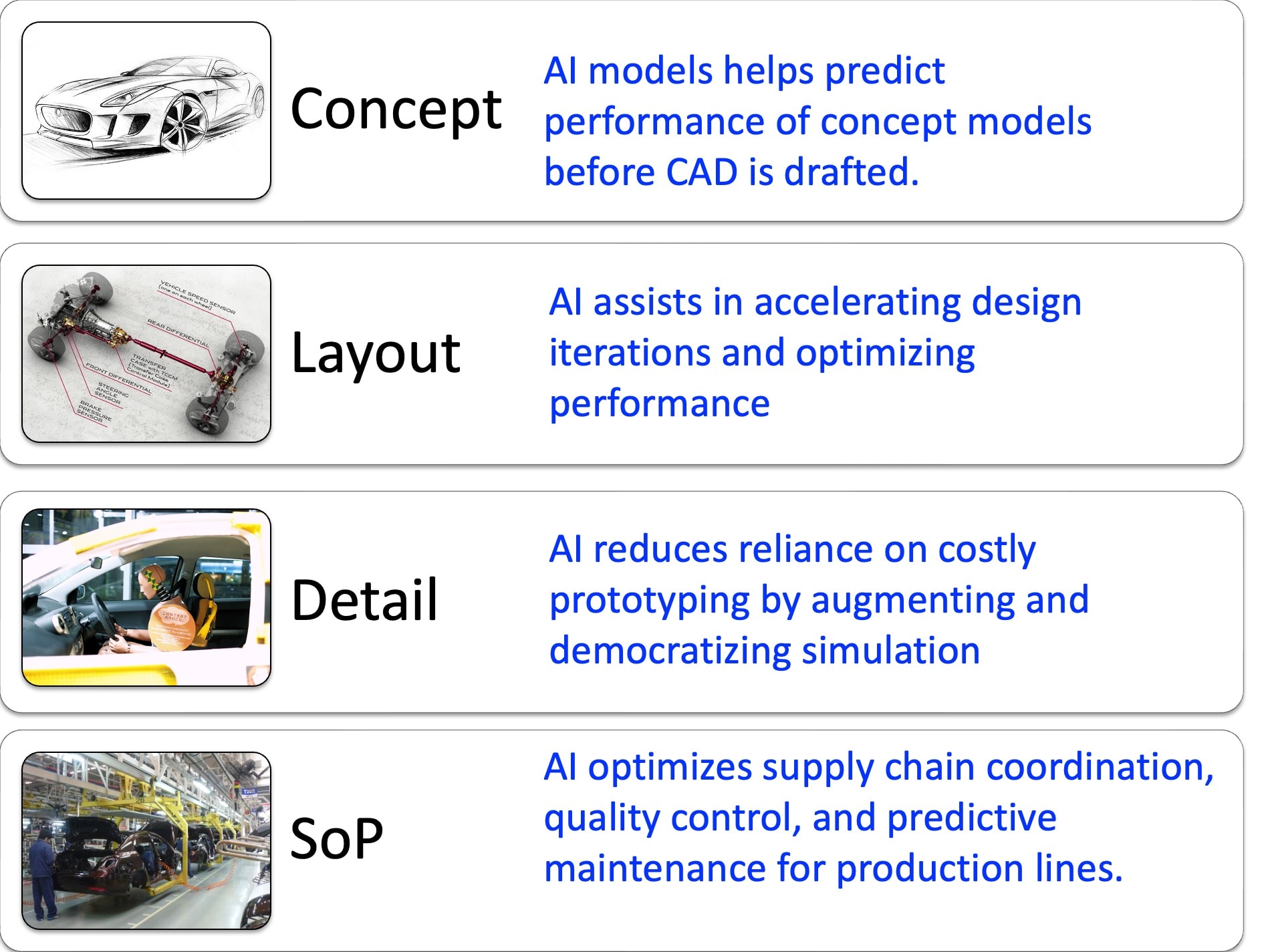
Conclusion and Way Forward
The traditional approach to automotive engineering often inhibits innovation needed for complex products. AI can solve the critical points of automotive product development by reducing costs and accelerating TTM, thus giving a competitive advantage to companies that adopt it earlier. From conceptualization to manufacturing, AI helps every phase by predicting outcomes faster than testing and simulation.
AI is not a one-size-fits-all solution—it is a set of specialized tools that enhance different phases of vehicle development. We have shown how AI accelerates engineering:
✔ Aerodynamics optimization – AI models trained on past CFD (Computational Fluid Dynamics) simulations suggest drag-reducing shape modifications in real time.
✔ Structural integrity assessment – AI-powered crash simulations analyze millions of scenarios, flagging weak points before physical prototyping.
Furthermore, in AI-driven demand forecasting helps OEMs anticipate shortages and adjust sourcing strategies accordingly (supply chain resilience).
AI is actively reducing costs, speeding up iterations, and enabling data-driven decisions.
We have shown use cases from Neural Concept. In next years, AI is likely to enable real-time, data-driven vehicle design and fully autonomous simulation environments. What is likely to change is the scale, speed, and autonomy of AI-driven design processes.
FAQ
What is the product development process in the automotive industry?
Product development typically follows four key phases: conceptual vehicle design, overall layout design, detailed design of components and assembly, and manufacturing under the OEM's brand.
Can AI integration reduce the need for physical prototypes?
Through virtual simulations, predictive modeling, and generative design, AI can reduce development time and costs. ML algorithms can analyze performance data and optimize designs before prototyping.
How is AI influencing the shift towards electric vehicles (EVs)?
AI accelerates EV development by optimizing battery management systems and improving energy efficiency. Machine learning simulations help engineers refine the thermal management of critical EV parts.