AI in Automotive Industry: Applications and Innovations
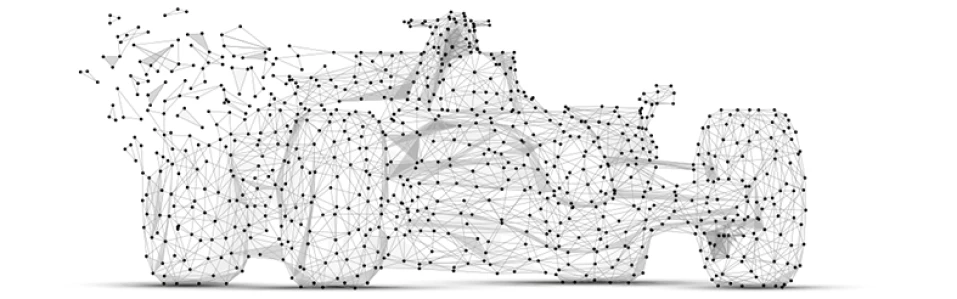
Artificial Intelligence now permeates every aspect of the automotive industry. For instance, it helps design workflows for vehicle aerodynamics or crash safety, for full vehicles or components. AI-assisted self-driving capabilities help to avoid hazards and improve traffic flow. In production processes, AI powers adaptable robots, predicts equipment failures, and detects defects invisible to humans, optimizing manufacturing processes. Deployed in cars, AI personalizes infotainment for connected cars based on customer preferences. With advanced safety features, it monitors driver fatigue and responds to spoken commands. Also, in the automotive industry, AI is leading the charge in transforming supply chain management, enabling more efficient and cost-effective operations.
This guide examines how these capabilities are transforming automotive systems and automotive businesses, the effect of Artificial Intelligence on product design, the remaining challenges for automotive manufacturers, and potential future breakthroughs for efficient vehicles.
In this guide, you will learn how AI enables real-time simulation for Tier 1 components and for full assemblies.
Introduction to AI in the Automotive Industry
Artificial Intelligence is reshaping vehicle development and operation from design and production to autonomous driving technology:
- Vehicle design: Simulation-driven optimization of powertrain and vehicle performance and safety: aerodynamics, crash safety, battery management, thermal comfort, and energy efficiency.
- Autonomous driving: Real‑time processing of camera, radar, and LIDAR data for navigation, obstacle detection, and adaptive decisions.
- Manufacturing: Smart robotics for assembly, predictive maintenance to prevent downtime, and automated quality inspection.
- User interaction: AI enhances the driving experience by providing personalized vehicle configurations based on individual driver preferences.
- Fleet operations: Route optimization, predictive diagnostics, and data‑driven maintenance scheduling to reduce costs.
- Service and updates: Generative AI tools for predictive failure analysis and automated repair recommendations.
This guide will cover:
- AI benefits
- Challenges for automotive companies
- Future prospects in the automotive industry.
These applications show how AI is already embedded across the automotive value chain, from design and manufacturing to fleet operations and the driver’s seat. But challenges remain, especially for design teams and supply chain management operating under increasing pressure.
Most of the AI benefits fall into two major areas: user experience and manufacturing operations.
1) User experience: Many of us already interact with AI daily as car drivers, through advanced driver assistance systems or connected vehicle features. Final users perceive AI through driving comfort and safety.
2) Manufacturing operations in car companies: Furthermore, behind the scenes of end-user deployment, automotive manufacturing is also benefiting from AI-driven IoT sensors in the production line to improve quality control beyond human capability.
The next step is understanding how to extend these advantages deeper into product design, engineering, and logistics.
In this article, you will learn the following about automotive manufacturing, autonomous driving technology, and other AI applications:
- Autonomous Vehicles and Self-Driving Cars
- What Technologies Enable Autonomous Vehicles to Navigate Complex Driving Challenges?
- Computer Vision in Autonomous Vehicle Technology
- How Does AI Enhance Safety Through Advanced Driver Assistance Systems (ADAS)?
- Manufacturing Processes and Computer Vision
- Where is AI Applied in Car Manufacturing?
- Supply Chain and Logistics Optimization
- From RFQ to Production
- Automotive Industry - Role of Tier 1 in the Supply Chain
- Who Are Tier 1 Suppliers in the Automotive Industry?
- AI in Customer Experience and Marketing
- Automotive Operations and Management
- What are the Practical Use Cases of AI Applied to Car Design?
- Automotive Industry Case 1 - Passenger Car Aerodynamics
- Passenger Car Aerodynamics: Reduce Resource Requirements
- Bringing Advanced Skills to more Resources and Without Toils: AI
- Automotive Industry Case 2 - F1 Car Aerodynamics
- What are the Practical Use Cases of AI Applied to Car Design?Challenges in F1
- Practical Case of Aerodynamic Design in F1 - Traditional Approach
- Aerodynamic F1 simulation
- Practical Case of Aerodynamic Design in F1 - AI Approach
- Automotive Industry Case 3 - HVAC Simulation
- How Data Comes to Help
- Retrieving and Using Data
- HVAC Case Summary
- Automotive Industry Case 1 - Passenger Car Aerodynamics
- Future of AI-Powered Vehicles
- Challenges and Considerations
- AI for Engineers in Car Companies
- How does AI Learn?
Autonomous Vehicles and Self-Driving Cars
AI-powered autonomy is reshaping how cars perceive and operate on the road to improve vehicle safety. Industry leaders invest billions to bring safe, reliable self-driving systems from labs to streets. These vehicles rely on real-time sensor fusion and AI algorithms to navigate complex environments with growing precision. The technology aims to reduce human error, improve traffic efficiency, and expand mobility options, especially for those unable to drive.
- Autonomous vehicles process data from cameras, lidar, radar, and ultrasonic sensors to identify obstacles, lanes, and traffic signs with high accuracy.
- Advanced AI enables split-second decisions for braking, steering, and acceleration, reducing accidents caused by human error.
- Through vehicle-to-vehicle and vehicle-to-infrastructure communication, autonomous systems can improve traffic flow.
- Self-driving technology promises greater independence for elderly and disabled passengers, reshaping urban transport and accessibility.
What Technologies Enable Autonomous Vehicles to Navigate Complex Driving Challenges?
Autonomous vehicles combine multiple AI-driven technologies to handle tasks like road navigation, obstacle avoidance, and real-time decision-making. Central to this is computer vision (CV), which interprets sensor data—from cameras, lidar, and radar to create a detailed understanding of the surroundings. AI algorithms identify objects such as pedestrians, other vehicles, and traffic signs, allowing the vehicle to respond appropriately while also helping to analyze customer data. This fusion of perception and analysis equips autonomous cars to operate safely and efficiently in dynamic environments.
Computer Vision in Autonomous Vehicle Technology
AI in the automotive sector extends beyond perception. Machine learning models process the visual data to track object movement, predict trajectories, and assess potential risks. Deep neural networks recognize complex patterns like the difference between a shadow and a physical obstacle, reducing false positives. This visual intelligence integrates with mapping systems and GPS to support lane keeping, adaptive cruise control, and automated parking.
Combined with other modules such as sensor fusion and path planning, computer vision forms the basis of autonomous navigation strategies.
How Does AI Enhance Safety Through Advanced Driver Assistance Systems (ADAS)?
AI enhances the driving experience by providing personalized vehicle configurations based on individual driver preferences. ADAS rely on AI and sensors to assist drivers and reduce accidents with proven, certified technologies:
- Adaptive Cruise Control: Uses radar and cameras to maintain a safe distance, reducing rear-end crashes by up to 20% (IIHS data).
- Lane Departure Warning: Detects unintentional lane drifting and alerts the driver, lowering single-vehicle accidents by 11%.
- Automatic Emergency Braking: Identifies potential collisions and applies brakes automatically, cutting front-to-rear crashes nearly in half.
- Blind-Spot Monitoring: Warns about vehicles in blind spots to prevent side collisions, improving lane-change safety.
- Driver Attention Monitoring: Tracks eye and head movements to detect drowsiness or distraction, prompting alerts to restore focus.
Regulators like NHTSA and Euro NCAP include these systems in safety ratings, driving widespread adoption and continuous AI improvements.
Manufacturing Processes and Computer Vision
AI-driven automation and CV are now integral to automotive production, delivering measurable improvements in quality and efficiency, as well as significant cost savings :
- Real-time Defect Detection: High-resolution cameras combined with deep learning algorithms identify surface defects such as scratches, dents, or paint inconsistencies with over 95% accuracy, reducing faulty outputs (examples include BMW’s visual inspection systems).
- Anomaly Detection: Machine learning models spot deviations in assembly processes, flagging issues like misaligned parts or incorrect torque application before defects reach the end of the line.
- Production Regulation: AI analyzes vehicle build data alongside sales trends to dynamically adjust production schedules, cutting inventory waste and ensuring just-in-time delivery (used by Toyota’s smart factories).
- Safety and Efficiency: Collaborative robots (cobots) equipped with AI vision systems safely assist human workers, adapting to changing environments and reducing workplace injuries.
- Sustainability: AI optimizes energy consumption on production lines by predicting peak loads and adjusting machine operation accordingly, supporting carbon footprint reduction targets.
Where is AI Applied in Car Manufacturing?
Artificial intelligence (AI) has many potential applications in car manufacturing. To name only three, examples: quality control, predictive maintenance, and supply chain optimization.
- Quality control – AI-powered CV inspects parts and assemblies in real time, detecting defects like surface scratches, misalignments, or paint flaws with high accuracy. This reduces errors and scrap rates while speeding up inspections compared to manual checks.
- Predictive maintenance – AI analyzes sensor data from manufacturing equipment to predict when machines are likely to fail or require servicing. This prevents unexpected downtime, extends equipment life, and lowers repair costs by enabling maintenance only when needed.
- Supply chain optimization – AI models forecast demand, track inventory, and optimize logistics routes. This improves just-in-time production, reduces stock shortages or excesses, and enhances responsiveness to market fluctuations, making the supply chain more efficient and cost-effective.
Supply and Logistics Optimization
- Inventory and Production Planning: AI algorithms analyze historical sales, supplier lead times, and demand patterns to maintain optimal inventory levels, reducing stockouts and excess inventory (as implemented by Ford).
- External Data Integration: By incorporating data from social media sentiment, weather forecasts, and market trends, AI powered tools refine production schedules and pricing strategies to anticipate disruptions and shifts in demand.
- Error Reduction and Automation: Automated order processing and shipment tracking minimize human errors and delays, improving delivery accuracy and customer satisfaction.
- Logistics Flow Improvement: AI-powered route optimization for inbound and outbound logistics reduces transportation costs and lead times while lowering emissions.
- Agility in Demand Response: ML models detect demand fluctuations early, enabling automotive companies to adjust procurement and manufacturing dynamically, enhancing market responsiveness and competitiveness.

From RFQ to Production
The RFQ phase marks the start of competition with suppliers, inviting Tier 1 companies to submit proposals for vehicle equipment sourcing by OEMs. Collaboration continues post-contract. The key difference between aftermarket and OEM supply is that aftermarket sells off-the-shelf parts, while OEM suppliers must adapt to evolving needs until and after SOP. OEMs require suppliers to meet functional specs like durability and energy efficiency. Until the 90s, physical prototypes and testing were used. Subsequently, CAE and CAD technologies reduced cycle times and costs, shifting from analogue to digital engineering (software 1.0), now entering a 2.0 digital revolution.
Automotive Industry - Role of Tier 1 in the Supply Chain
Let’s take a step back before speaking about AI technology. We will look at the organization of the supply chain in the automotive industry. We will identify where AI technology can help in any automotive sector.
Who Are Tier 1 Suppliers in the Automotive Industry?
Tier 1 suppliers are companies that provide critical components or systems directly to Original Equipment Manufacturers (OEMs) in the automotive sector, whether for traditional, hybrid, or electric vehicles. Unlike commodity suppliers, Tier 1 suppliers are strategic partners rather than simple "vendors".
OEMs rely on Tier 1 suppliers to add value, not just deliver parts. This means Tier 1 companies must demonstrate strong design and manufacturing expertise. Their competence is both a power and a responsibility: they influence vehicle performance, innovation, and overall quality, while also being accountable to the OEM for meeting strict technical and delivery standards.
In short, Tier 1 suppliers are essential collaborators in the automotive value chain, bridging advanced engineering capabilities with OEM needs.
AI in Customer Experience and Marketing
Customer Data Platforms (CDPs) integrated with AI provide automotive brands with a 360-degree view of their customers, facilitating personalized experiences. For example, a dealership group might integrate sales history, online browsing patterns, and used car inventory into a single AI-enhanced dashboard.
Automakers use AI algorithms to analyze customer data, allowing them to create personalized marketing strategies. This could mean sending targeted offers for hybrid models to customers who have shown interest in fuel-efficient vehicles, or promoting premium trims to those who value luxury features.
AI-powered chatbots can provide customers with quick responses and help them find the right choice for their needs in the car inventory. A shopper browsing an SUV page at midnight could ask a chatbot about vehicle data such as towing capacity, compare models, or even schedule a test drive without waiting for human staff.
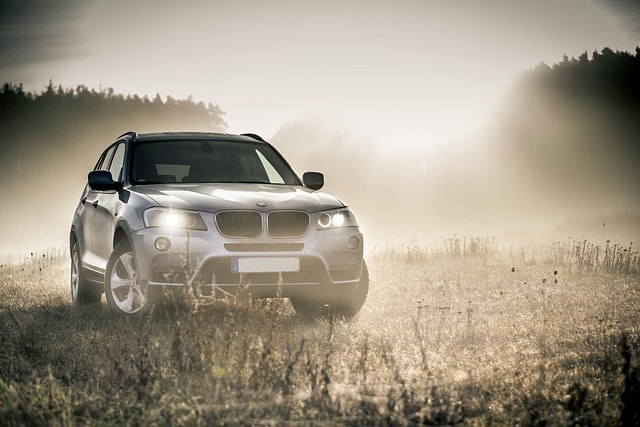
AI allows car dealerships to operate round-the-clock customer service, improving interactions with customers. Whether it’s answering finance questions at 3 a.m. or sending a personalized reminder for an upcoming service appointment, AI keeps the customer relationship active and responsive at all hours.
Automotive Operations and Management
AI in the automotive sector integrates perception, prediction, and control systems to enable autonomous operation. Together, these components create a closed-loop decision process that allows vehicles to navigate urban traffic, highway speeds, and driving conditions with minimal human intervention.
- Data-driven decision support
- Instead of broad demographic guesses, AI models can process warranty claims, driving pattern telemetry, and after-sales service logs to reveal correlations between component wear, environmental conditions, and driver behavior. This allows engineering and product teams to adjust designs, plan targeted recalls, or schedule preventive maintenance with precision.
- Integrated production monitoring
- Computer vision and sensor fusion systems detect surface defects, misalignments, or assembly anomalies in milliseconds. This shifts inspection from batch sampling to continuous, real-time verification, reducing rework cycles and cutting scrap rates.
- Supply chain management and synchronization
- Predictive algorithms use order histories, parts lead times, and logistics data to forecast shortages or bottlenecks before they impact the line. This enables production planners to dynamically reroute orders, adjust shift patterns, or alter build schedules without halting assembly.
- Adaptive manufacturing lines
- AI-driven control systems can modify the robot trajectory, speed, and tool usage in real time based on sensor feedback and production requirements.
What are the Practical Use Cases of AI Applied to Car Design?
We will detail three practical use cases of AI in vehicle design: passenger car aerodynamics, F1 car aerodynamics, and HVAC simulation. Many more applications exist, such as structural optimization, battery thermal management, and crash simulations.
- Passenger Car Aerodynamics – AI-driven surrogate models accelerate CFD analysis of external airflow, enabling multi-objective optimization of drag coefficient, lift, and vortex structures directly from CAD geometries.
- F1 Car Aerodynamics – ML algorithms process high-fidelity RANSE (and DES, LES) simulation data to predict turbulent wake interactions and optimize aerodynamic components for maximum downforce with minimal drag penalty.
- HVAC Simulation – AI integrates steady state or transient CFD thermal models with occupancy and climate data to optimize airflow distribution, heat transfer, and energy consumption in cabin climate control systems.
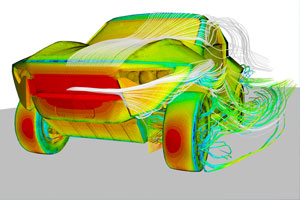
Automotive Industry Case 1 - Passenger Car Aerodynamics
Aerodynamic design of a passenger car can be tackled with aerodynamic simulations (CFD) or AI predictions. We will review three topics that impact battery/fuel consumption, vehicle handling, and driver/passenger comfort: drag, downforce, and (aero)acoustics. Software such as CAE / CFD can simulate all of this within hours or days. With AI, it is possible to get answers with AI within seconds on several aspects:
- Optimize Drag
- Reducing a car’s drag boosts fuel efficiency and speed. Methods include streamlining and active aero devices like spoilers and air dams, which we'll discuss further. Aerodynamic devices such as spoilers can contribute to better performance in terms of downforce and aerodynamic resistance
- Optimize Downforce
- Generating downforce (negative lift) can help improve the vehicle's handling and stability at high speeds or in specific situations such as curves. This can be achieved using active aerodynamic devices such as spoilers and airfoils.
- Optimize noise
- A source of annoyance for drivers and passengers is internal and external noise. External noise is generated by air flowing around the car and specific devices such as side mirrors (see figure). The aerodynamic design of a car should consider the noise generated by the airflow around the vehicle to reduce it.
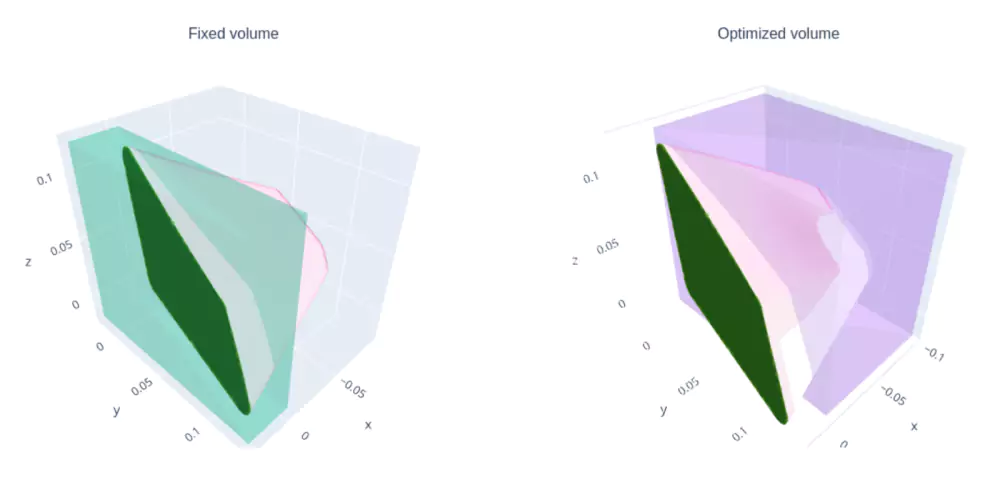
Passenger Car Aerodynamics: Reduce Resource Requirements
All topics boil down to KPIs that need optimization: drag minimized for consumption, downforce maximized for stability, and aeroacoustic noise minimized for comfort. While CFD simulations can support optimization, they require many hardware resources and specialized skills, accessible to only a few designers.
Bringing Advanced Skills to more Resources and Without Toils: AI
AI learning helps engineers use CFD effectively, matching simulations, and supports non-CFD specialists on local computers. This is excellent news for the auto industry, where “AI in automotive’ often meant robots or self-driving cars. AI’s impact will reach the automotive value chain sooner, beyond just autonomous vehicles.
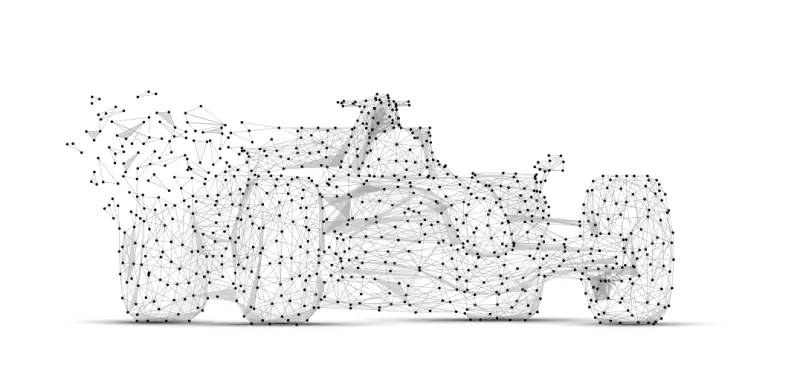
Automotive Industry Case 2 - F1 Car Aerodynamics
In Formula 1, from the aerodynamic point of view, there are 4 major challenges. AI in the Automotive sector, and specifically Aerodynamics, can help solve them.
Challenges in F1
In an F1 car, designers focus on creating as much downforce as possible while sustaining straight-line speed. This allows the driver to have a better grip and to handle through turns, a crucial factor for automotive companies focusing on performance. Downforce is so powerful that it could enable driving on a ceiling!
Reducing drag force is also essential because it can help increase the car’s top speed: know more on F1 aerodynamics!
Another aspect, more relevant than in passenger cars, is aeroelasticity. The F1 car has numerous external structures exposed to aerodynamic loads. The car’s body and wings can flex and deform under such loads, which can affect the car’s performance, as seen in a few spectacular accidents.
A final crucial point in AI development is Regulations. F1 has strict rules on car aerodynamics, including wing shape, diffusers, and aerodynamic devices. These can limit design options. There are also limits on wind tunnel testing runs and CFD simulation hours for car development. This is different from car manufacturers, where external controls do not regulate resource usage.
Practical Case of Aerodynamic Design in F1 - Traditional Approach
Let us now investigate the case of an F1 designer who needs to examine five different car designs as in the figure (superposed).
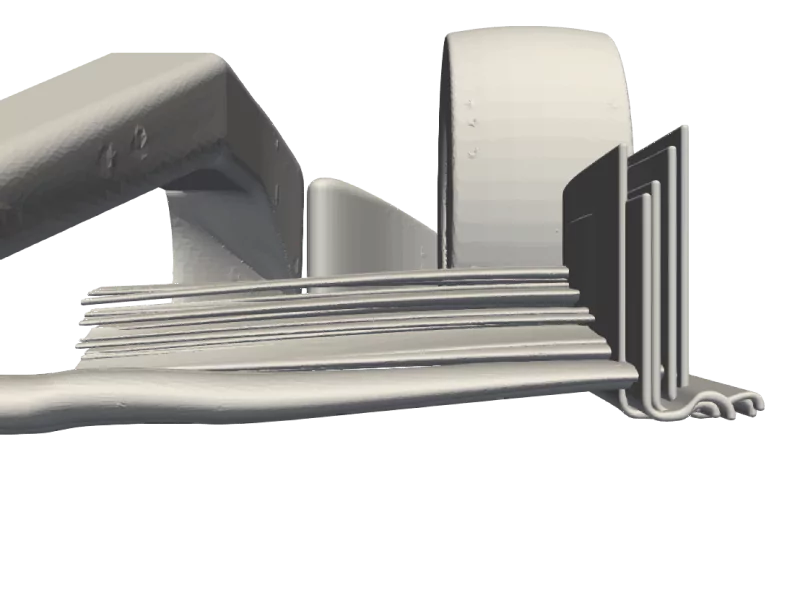
Traditionally, the designer would iterate with her CFD department in order to continuously have insights into what is virtually happening in the flow field (figure below) and computed aerodynamic parameters such as the downforce.
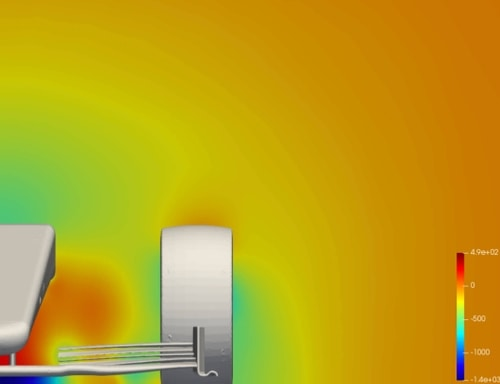
Aerodynamic F1 simulation
Traditional simulation approaches require a transition from CAD to CFD images handled by specialists, which can be time-consuming. A more advanced scenario involves users uploading CAD files via a web portal and receiving automated aerodynamic reports, where response time remains crucial.
Practical Case of Aerodynamic Design in F1 - AI Approach
Can AI reduce the simulation 3-hour wait to 0.3 seconds? This would enable designers to handle multiple design orders, exploring a broader, detailed space with AI. Thus, they can focus on final solutions using CFD or wind tunnel tests. Designers need surface and volumetric data, especially surface pressure, shown below. For instance, pressure and velocity fields in vehicle cross-sections. AI allows checking aerodynamics quickly, i.e., 0.3 seconds on a laptop versus 3 hours on an expensive HPC cluster. The key is that CFD solver time drops dramatically with AI predictions, and meshing is virtually eliminated.
An F1 car’s cross-section with streamlines compares CFD (ground truth) and AI predictions, illustrating how this capability will soon transform F1 and other CFD or FEA uses in automotive and yacht racing.

Automotive Industry Case 3 - HVAC Simulation
Computational fluid dynamics (CFD) simulation can be used to optimize the design of a car's heating, ventilation, and air conditioning (HVAC) system by predicting how the air will flow through the system and how it will affect the temperature and comfort of the occupants.
However, CFD is an expert topic reserved for a few specialists and only for some HVAC designers; as it is the case throughout the automotive industry. How can AI technology help HVC designers? Can AI in the automotive industry bridge the gaps between customers (OEM), designers and simulation specialists?
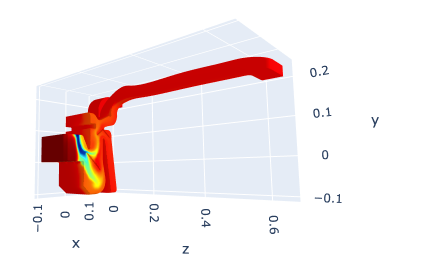
How Data Comes to Help
Big data coming from years or decades of experience in the auto industry, coupled with recent advances in AI and machine learning, is transforming the automotive industry for next-generation cars and can come to help HVAC designers in two ways:
- Fast thermal and flow predictions associated with designs with AI-based algorithms. AI algorithms can be used to build data-driven predictive models that can estimate the performance of an HVAC system based on its design and ambient temperature conditions. These models can help designers optimize the size and configuration of the system.
- Creation of new designs (optimization) with an AI-powered system. AI optimization algorithms can be used to search for optimal solutions based on a set of constraints and objectives, and, again, on the previous AI predictive capabilities. These algorithms can consider many design variables in almost real-time and find the best combination that meets the desired performance targets.
If you want to see how AI can revolutionize comfort and efficiency, check out our deep dive into the optimal design of an HVAC system.
Retrieving Data and Using Them
We examine an HVAC simulation case using Neural Concept’s platform, which leverages datasets from the company’s historical data stored in the PLM, including CAD, simulation, and sensor data. In HVAC design, inputs like CAD geometries and operating parameters (e.g., inlet flow and temperature) are fed into AI, predicting air pressure, velocity, and temperature in 3 seconds. This tool offers an integrated workflow within the design environment, tailored to users’ needs.
HVAC Case Summary
AI is a “Software 2.0” approach, using CAD and CFD inputs instead of physics first principles.
Note that Case History N°1 data is smaller than expected: AI achieved accuracy with just 100 samples instead of 1,000 or more. Key to efficiency was using Neural Concept’s platform for non-parametric CAD reading and transfer learning to restart from a pre-trained model.
Future of AI-Powered Vehicles
- Full autonomy in controlled environments – AI systems will first achieve reliable self-driving in geofenced, low-complexity routes such as industrial sites, ports, and dedicated urban lanes.
- Advanced driver monitoring – Real-time detection of driver distraction, drowsiness, or medical emergencies through in-cabin cameras and physiological sensors.
- Predictive maintenance – AI models will forecast component wear and failures, reducing downtime and cutting fleet maintenance costs.
- Fleet-wide learning – Vehicles will share driving data to continuously improve AI decision-making across entire fleets, accelerating software updates.
- Integration with smart infrastructure – AI-powered vehicles will coordinate with connected traffic lights, dynamic road signs, and automated charging stations for smoother traffic flow.
What Are the Challenges and Considerations of AI in the Automotive Industry
The challenges and considerations of AI in the automotive industry are numerous:
- Cybersecurity – Autonomous driving systems can be hacked to disable braking systems or alter navigation routes. Example: In 2015, researchers remotely took control of a Jeep’s steering and transmission.
- Data Privacy – Vehicles collect driver location, biometric, and behavior data. Breaches could expose sensitive patterns (e.g., home address, daily commute times).
- Safety Failures – CV can misinterpret objects in poor weather, leading to incorrect braking or acceleration.
- Ethical Decisions – In unavoidable crashes, AI must choose between conflicting safety outcomes, raising public trust issues.
- Workforce Impact – Automated driving and maintenance systems reduce demand for human drivers and certain repair jobs.
- Transparency – Black-box AI models make it hard to explain why a vehicle made a specific maneuver, complicating accident investigations.
AI for Engineers in Car Companies
There are probably, in most companies, 10 to 100 times more design engineers than specialized CFD and CAE engineers. Mass deployment of CFD and CAE is conceivable with AI-based simulation, leading to significant cost savings. These are the three main enablers making AI-based simulation democratic and therefore mass-deployable.
- AI can be deployed in a platform for design engineers who do not need to be experts in AI.
- Thanks to an artificial network structure, AI acts in seconds instead of hours or days
- AI processes industrial geometries (CAD) without requiring time-consuming and specialist software such as "meshers" or solvers.
Therefore, the final deployment of Deep Learning from tech companies such as Neural Concept is not easy... it is simply straightforward!
How does AI Learn?
AI learns by adjusting internal parameters to reduce errors when predicting outputs from inputs.
In the automotive sector, Convolutional Neural Networks (CNNs) can identify patterns in 3D CAD models and correlate them with simulation data like CFD or FEA results. This opens the door to faster, more accurate design decisions: see our guide to 3D CNNs for Engineers.
A CNN is a neural network for image recognition, with layered neurons analyzing visual data hierarchically. Basic features are recognized by lower layers, while higher layers interpret complex patterns. This process, shown in the figure, learns more details from left to right. CNNs are effective for image classification, and associating engineering results with CAD inputs is a very advanced form of this.
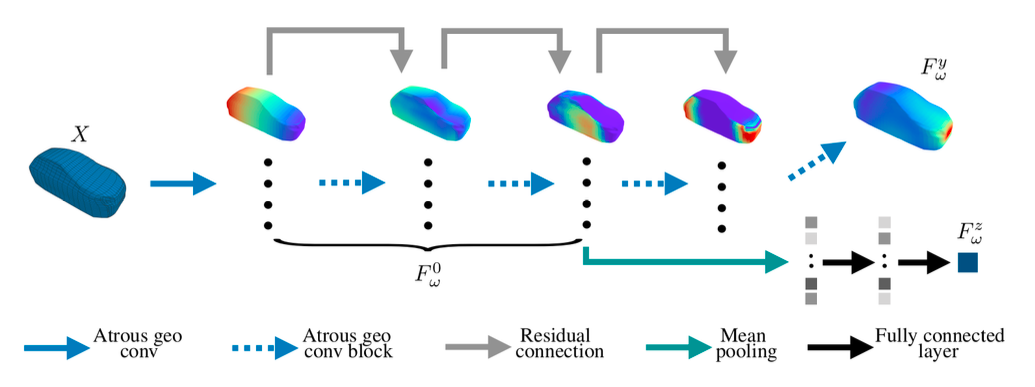
Conclusion
Based on this comprehensive analysis of Artificial Intelligence in the automotive industry, here are the key conclusions:
- Current Impact: AI is already transforming automotive operations across the entire value chain - from design optimization and manufacturing quality control to self-driving cars and customer experience enhancement.
- Design Acceleration: Generative AI product design reduces simulation times from hours to seconds, enabling much broader design exploration. Cases show aerodynamic optimization, F1 development, and HVAC design becoming accessible to non-specialists.
- Manufacturing Revolution: AI-powered CV achieves 95%+ defect detection accuracy, while predictive maintenance prevents costly downtime. Smart robotics and automated quality inspection are optimizing production efficiency.
- Future Outlook: Full autonomy in controlled environments and fleet-wide learning will drive the next phase of innovation.
- Key Challenges: Cybersecurity vulnerabilities, data privacy concerns, safety validation, and workforce displacement remain critical considerations for widespread adoption.
AI’s democratization of advanced engineering capabilities represents a fundamental shift toward “Software 2.0” approaches in automotive development.
FAQ
How is Artificial Intelligence implemented in automotive manufacturing processes?
AI is used for real-time defect detection via CV, predictive maintenance by analyzing equipment sensor data, and dynamic production scheduling informed by sales and inventory analytics.
What are the differences between traditional approaches and AI in the automotive industry?
Traditional automation follows fixed, pre-programmed tasks, while AI enables adaptive decision-making, learning from data to handle variability and optimize processes without human intervention.
What are the applications of Artificial Intelligence in vehicle safety?
AI powers features like automatic braking, lane departure warning, blind-spot detection, and driver attention monitoring to prevent accidents and enhance driver awareness.
How is Artificial Intelligence used in self-driving vehicles?
Artificial Intelligence fuses data from sensors (camera, lidar, radar) to perceive the environment, interprets complex scenarios, and makes real-time driving decisions such as steering, braking, and acceleration, enhancing autonomous driving capabilities.
What is the difference between Artificial Intelligence and ML in automotive applications?
Artificial Intelligence is the broad concept of machines performing tasks that require intelligence; machine learning is a subset where systems learn from data to improve performance in applications like vision recognition and predictive analytics.