Cold Plate Design Explained: Examples and Optimization
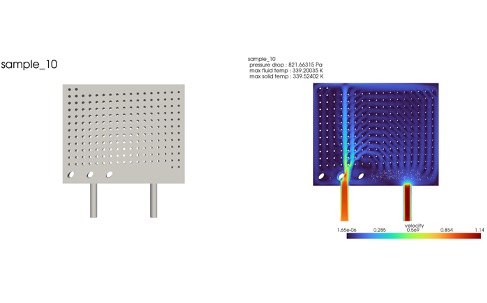
In engineering, we have to deal with unavoidable heat sources. Cold plates are our little friends, giving a big help in transferring energy from thermal sources to cooling systems. Cold plates remove the "heat load" on sensitive parts of a mechanical or electronic device via liquid cooling. Liquid cooling is particularly efficient where a standard forced convection cooling system would take too much space. Thus, shrinking spaces and increasing powers call for help from cold plates!
This article on cold plates aims at an initial understanding of the principles of heat transfer of these thermal management systems. Engineers design cold plates with the help of mathematics and computational software; they select materials, optimize flow dynamics, and evaluate heat exchanger efficiency. Engineers focus on achieving optimal heat exchanger performance for the liquid cold plate designs and overall system thermal stability.
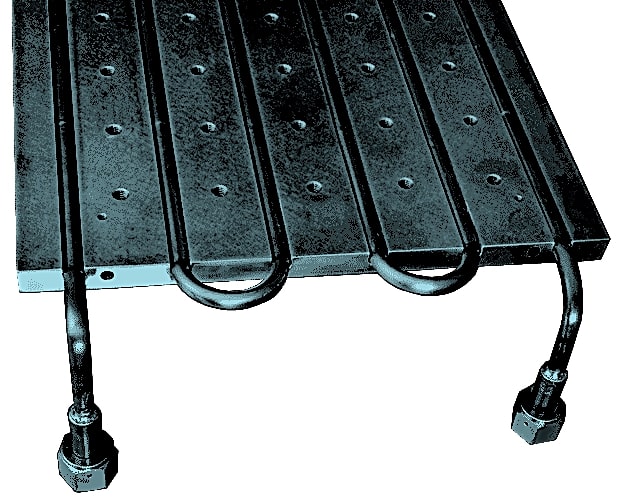
As we can see from the figure, the cold plate is connected to a larger system through inlet and outlet plugs. The liquid cooling system operates as a circuit comprising the cold plate itself that interacts with the heat source, a pump that moves fluid throughout the system, and a heat exchanger (HX) that ultimately releases the thermal energy from the liquid, often with the help of a forced convection device (a fan).
The article will review the principles of airflow and liquid cooling, the parameters usable in tuning design, and how the cold plate is linked to additional remote devices such as radiators. HX systems are part of devices impacting our daily lives, helping transfer thermal energy. Their knowledge is also interesting for non-experts since high heat loads disrupt mission-critical operations, such as satellites or data centers.
Also, we'll shortly review the techniques engineers use to predict a cold plate solution before it's physically constructed - namely CAD, CAE, and the recent Deep Learning AI prediction approach.
Industrial Examples of Cold Plate Usage for Thermal Management
Examples of systems where a cold plate is mounted are from diverse industries: automotive, aerospace and defense, ICT and various energy or machinery applications. Let's review them quickly.
Automotive Cold Plate Examples
In electric vehicles, cold plates are employed, for example, in the thermal management of battery packs. Maintaining an appropriate range of temperatures enhances battery longevity and performance while safeguarding against overheating and related safety issues, an important cold plate function.
Note that both of the following cooling methods are used in vehicles for thermal management, either traditionally endothermic or EVs:
- Air cooling typically uses fans to dissipate thermal energy (we will use this term as equivalent to "heat" throughout the article) with forced convection. In EVs, it is applied electric motor and power electronics (e.g., inverters and DC-DC converters)
- Liquid cooling utilizes cooling fluids (water or specialized liquids) to remove thermal energy from the battery cells, engine, or other overheated parts. Liquid cooling is characterized by better transfer and removal of excess thermal energy. However, the liquid cooling carrier or coolant may be subjected to critical events, such as boiling, to be prevented since they represent a local collapse in thermal performance. Li-Ion battery cells' high energy density and thermal energy generation in EVs make liquid cold plate cooling an efficient choice for maintaining the battery's temperature within a safe and optimal range. Liquid coolant circulates through channels or tubes integrated into the battery pack, absorbing and taking care of high heat loads via a liquid cold plate.
These two cooling methods are frequently employed individually or in combination to manage and regulate temperatures effectively.
A traditional example of such a combined air cooling and liquid cooling approach in vehicles can be found in the design of a radiator with an integrated fan, which dissipates high heat loads absorbed by the vehicle's liquid cooling circuit from the endothermic engine. At the same time, a pump moves the liquid cooling substance.
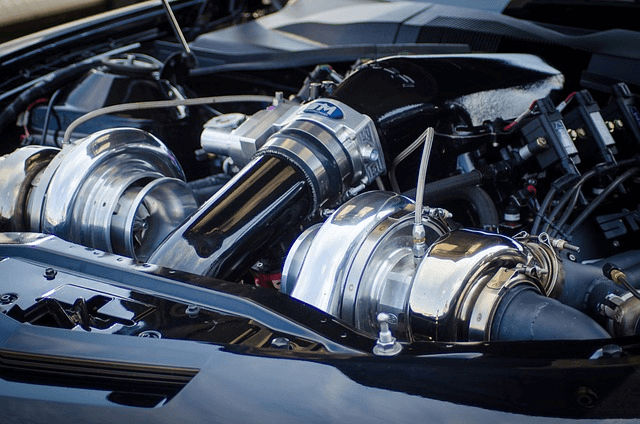
Aerospace and Defense Cold Plate Cooling Examples
Aerospace Electronics Liquid Cooling
Aerospace applications, including avionics and satellite systems, can rely on cold plates to control the temperature of critical electronic systems in the harsh conditions of space for satellites and high-altitude flight. While liquids can work in space for cooling and heat transfer, the mechanisms and systems are adapted to the unique microgravity and vacuum environments.
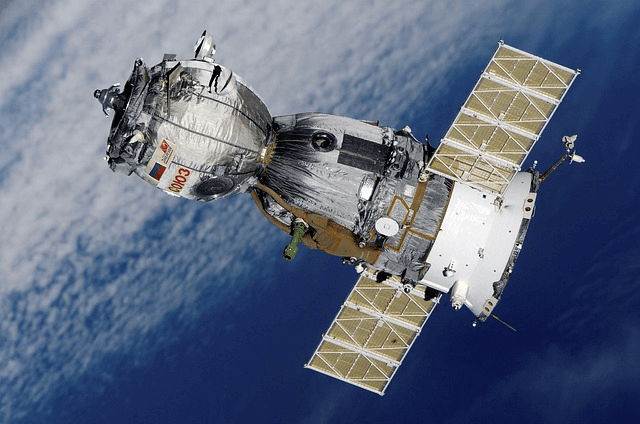
Military and Defense Electronics
Military applications, including radar systems and communication equipment, often integrate liquid cooling systems and cold plates to maintain the operational readiness of electronic components in extreme ambient or operating conditions.
Energy Machinery Cold Plate Cooling Examples
Industrial Power Electronics
Industrial machinery and power electronics often incorporate liquid cold plates to cool high-power semiconductors such as insulated gate bipolar transistors (IGBTs) and thyristors when confined in restricted spaces. This ensures efficient operation with high heat loads thanks to the cold plate.
Cold Plate Application in Renewable Energy Inverters
Inverters in renewable energy systems, e.g. solar or wind power converters, rely on cold plates for efficient cooling.
This enhances the energy conversion efficiency while extending the lifespan of critical components.
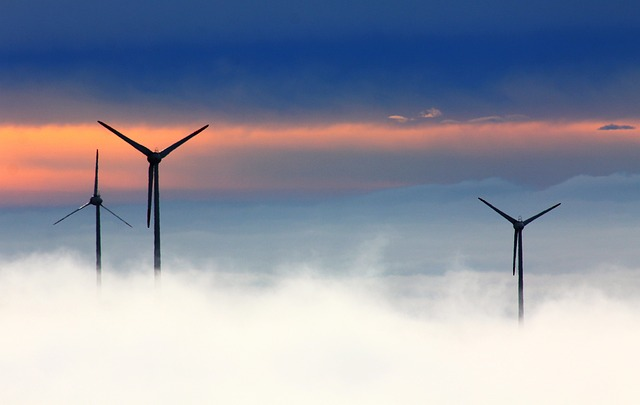
ICT applications - Cold Plate Cooling Examples
Role of the Cold Plate in Telecommunications Infrastructure
Cold plates are employed in data centers and telecommunications infrastructure to manage the heat generated by networking equipment, ensuring uninterrupted data transmission and system reliability.
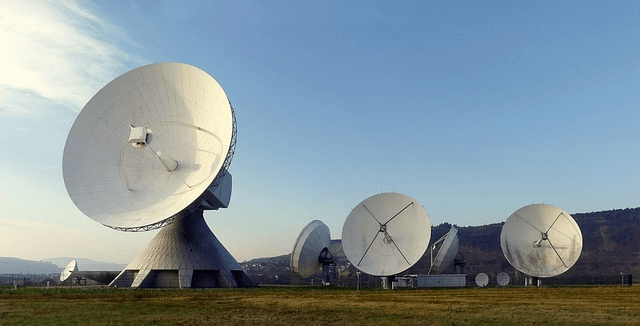
Role of the Cold Plate in High-Performance Computing (HPC) Clusters and Data Center Cooling
An HPC Cluster is a powerful computing infrastructure that handles computationally intensive tasks, simulations, scientific calculations, and data analysis. Cold plates and tubes are integrated into HPC clusters to cool powerful processors and high-density memory modules, ensuring sustained computational performance.
The role of cold plates is crucial in HPC clusters and data center cooling due to the high heat loads generated during computations and other operations, both with CPUs and GPUs.
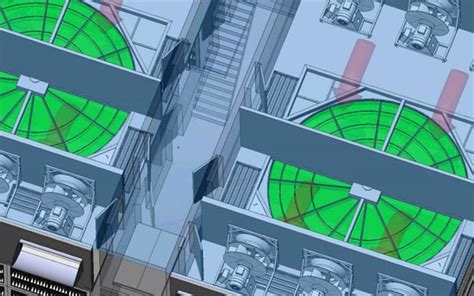
Heat Conduction in Air or Liquid Cold Plates
Liquid cold plates leverage conduction in the metal plate to efficiently transfer heat from the heat sources to the cooling fluid gaseous or liquid).
So, we want to know the rate Q (in W) at which thermal energy is transferred, expressed as a function of the solid material's thermal properties (such as the conductivity of the cold plate material, its cross-sectional area, and its thickness). This would be useful when designing heat sinks, calculating insulation effectiveness, or sizing components in thermal management systems where conduction is critical.
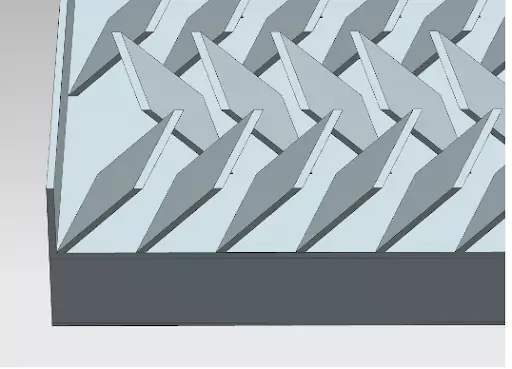
The sought relationship is Fourier's Law of Heat Conduction, in W:
Q = -k A ΔT / d
- k is the thermal conductivity of the cold plate material, in (W/m·K)
- A is the cross-sectional area for heat transfer in m²
- d is the thickness of the cold plate in m
- ΔT is the temperature difference between the thermal source and the liquid cooling system fluid in K.
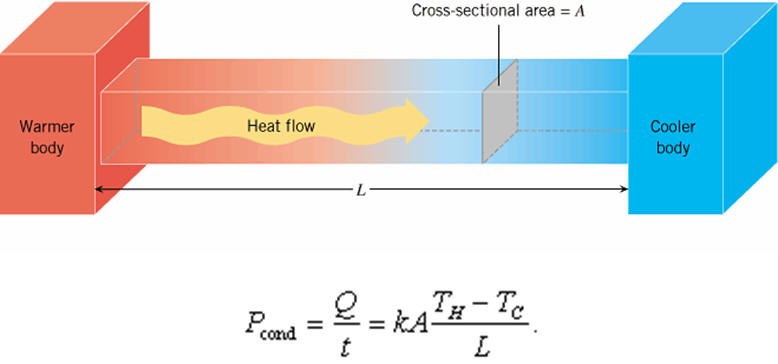
Material Selection in Cold Plates
The choice of material for constructing the cold plate is essential. Materials with high thermal conductivity, such as copper or aluminum, are commonly used due to their ability to conduct thermal energy efficiently. For example, pure copper has a k conductivity of over 400 W/m/K. Interestingly, copper's high thermal conductivity is the second highest (after silver) among pure metals at room temperature. Copper's excellent electrical conductivity parallels this. The thermal properties of these materials play a significant role in determining the cold plate solution's effectiveness.
In more complex geometries or situations involving non-uniform temperature distributions, the equation may need to be adapted or replaced with more complex equations, such as the conduction equation in cylindrical or spherical coordinates, to model the transfer of thermal energy accurately, or even CAE (Computer-Aided Engineering) software for numerical solution.
Basic Fluid Dynamics and Flow Optimization of Cold Plates
Engineers design the internal passages within cold plates to optimize the flow of the coolant. Fluid dynamics principles, including the (incompressible) Navier-Stokes equation, are instrumental in designing passages that facilitate efficient transfer while minimizing pressure drop ΔP.
Let us translate into mathematics the following concept:
"time rate of change of velocity" + "convective term" = "pressure gradient" - "viscous dissipation" + " gravitational force"
The equation is:
ρ ∂v/∂t + (v ⋅ ∇) v = -∇ p + μ ∇² v + ρg
- ρ represents the density of the coolant (in most cases constant)
- v is the velocity vector in the coolant (i.e. with 3 components u, v, w)
- p denotes pressure
- μ is the dynamic viscosity of the coolant (NB the cooling system could be water or other substances with better properties)
- g is gravitational acceleration (NB the system could operate under microgravity conditions)
- ∇ is the gradient vector operator, and ∇² is the scalar Laplacian operator
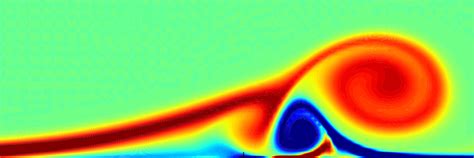
We need boundary conditions and initial conditions for both velocity and pressure, to obtain a unique solution for flow.
Solving this system of equations numerically, often using Computational Fluid Dynamics (CFD) methods, allows us to determine the velocity and pressure distribution in the computational flow domain over time.
To solve this equation for flow within a liquid cold plate, you must simplify it based on its specific geometry and boundary conditions. In most cases, the simplification will involve making certain drastic assumptions, such as:
- steady-state flow (ignoring the time-dependent term ∂v/∂t)
- incompressible flow (ρ is constant)
- neglecting body forces like gravity (g) for horizontal cold plates.
The choice of boundary conditions, such as the inlet velocity and pressure, will also depend on the cold plate's specific design and operating conditions.
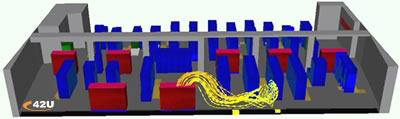
Analytical solutions to the full Navier-Stokes equations are challenging or impossible for most practical engineering problems involving complex geometries, unsteady flow, turbulence, or multiphase flow. Numerical methods like Computational Fluid Dynamics (CFD) are essential for solving and analyzing fluid flow behavior. CFD discretizes the governing equations and solves them numerically over a computational domain, making it possible to handle a wide range of real-world scenarios.
Prediction with CFD and AI
Ideally, one would expect that simulation tools are ready to be plugged into design tools such as CAD and deliver instantaneously quantities of interest for the designer, such as for an HX:
CAD ==> [max Temperature in the solid, max Temperature in the fluid, pressure loss ΔP in the system]
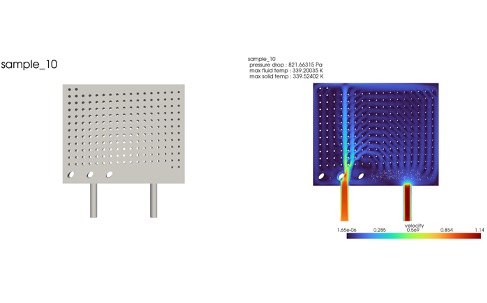
However, in reality, with CFD or FEA tools, the time represented by the arrow "==>" corresponds to hours or days. How do we shorten design iterations?
The background data science and AI details have been covered elsewhere; here, suffice it to say that the intuitive expectations can now be fulfilled thanks to...:
1) the large amounts of data cumulated by engineers over the years;
and
2) the capability of Deep Learning to learn to recognize shapes and associated KPIs, therefore both geometrical details of any HX, and associate it with the thermal performance data stored by engineers.
Thus, when facing a new shape, designers should no longer fear long wait times from CAE to get an answer on the needed engineering KPIs.
![AI can predict in 0.1 - 1 second the engineering KPIs such as [max T_solid, max T_fluid, ΔP] for this exchanger!](https://cdn.prod.website-files.com/60d07e2eecb304cb4350b53f/651ee3cc77fc8afd708ea218_57d9d6b8-bda0-4967-843e-76665aaacd41.png)
Heat Exchanger Efficiency
Liquid cold plates essentially function as an HX. The effectiveness of the exchange process can be quantified by the effectiveness-NTU (Number of Transfer Units) method, which considers the heat capacity rates of the cold plate and the cooling fluid.
The following equation represents a measure of how well the HX is performing in transferring heat from one fluid to another:
ε = 1 - exp ( -NTU * (1 + C_r))
The Number of Transfer Units (NTU) is a dimensionless parameter that accounts for the heat transfer surface area, the overall HCT (coefficient of heat transfer), and the flow rates of the two fluids. It quantifies the relative size of the HX and characterizes its thermal performance. The ratio of the capacity rate of the cold plate (usually the cold fluid) to that of the hot fluid (cooling fluid) is C_r.
Custom Cold Plate Design - Optimization Challenges
We have seen the basic underlying physical principles of a liquid cold plate, but you may wonder what is a cold plate and how we can conceive optimal designs for the cold plate's thermal performance.
The cold plate and other advanced thermal solutions in thermal management are heavily based on specific geometric configurations. These geometrical design criteria are fundamental in tailoring cold plates for diverse applications, from high-performance computing to industrial equipment. A well-designed cold plate efficiently removes high heat loads and ensures the reliability and longevity of critical components within thermal management systems.
The overall shape of the liquid cold plate is tailored to fit the specific thermal source and system constraints. Whether flat, curved, or customized to fit a particular component, geometry must be carefully designed to ensure efficient thermal contact.
In the following section, we'll examine the key geometrical design criteria for cold plates.
Cold Plate Channel Geometry and Layout
The configuration and dimensions of internal coolant channels within the liquid cold plate significantly impact its performance.
Engineers design these channels considering factors like width, depth, and spacing to maximize the surface area in contact with the energy source while maintaining uniform flow in the liquid cold plate.
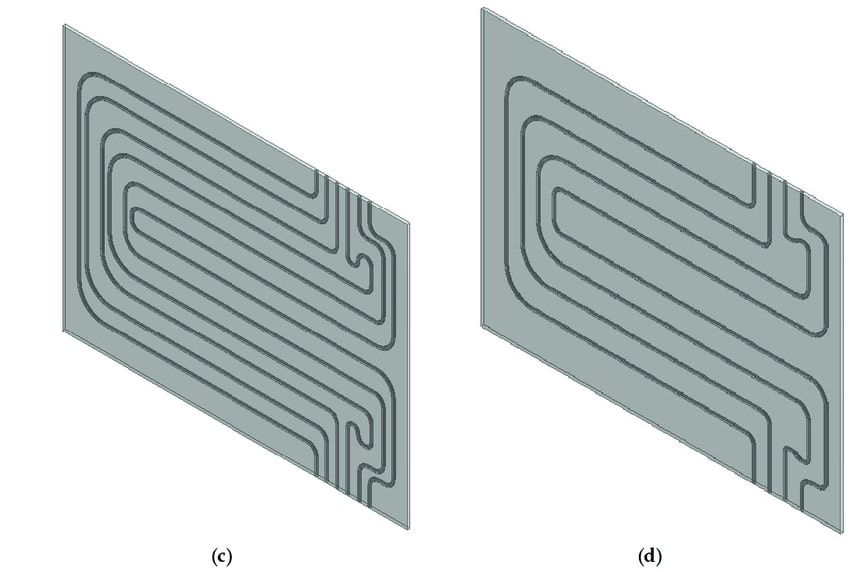
The shape of the channels, whether rectangular, circular, or other profiles, can affect the velocity distribution and ΔP. Optimizing the cross-sectional geometry is vital for achieving efficient thermal energy removal by the liquid cold plate.
Since the arrangement of channels on the cold plate surface is crucial, engineers explore various layouts, such as serpentine or parallel configurations, to efficiently distribute coolant and ensure uniform energy dissipation.
Fin Structures in Heat Exchanger Design
Fin structures increase the available surface for thermal dissipation. The geometry of these fins, including height, thickness, and spacing, is tailored to the specific application's thermal requirements.
What are the main fin parameters, and what is the contribution to the optimized liquid or air-cooling cold plate design?
- Fin Height: The height of the fins, measured perpendicular to the cold plate's surface, is adjusted to balance the need for increased area with practical considerations such as the available space within the cold plate. Taller fins generally provide a greater exchange area.
- Fin Thickness: The thickness of the fins, or the dimension in the direction parallel to the cold plate's surface, is fine-tuned to optimize conduction and distribution. Proper thickness ensures efficient thermal coupling between the hot components and the cooling liquid or air flowing through the channels.
- Fin Spacing: The spacing between individual fins facilitates optimal airflow and channel flow. This spacing minimizes resistance to liquid or air movement while maximizing convective HTC.
Inlet and Outlet Locations
Positioning the cooling material's inlet and outlet ports on the cold plate can influence liquid or air distribution and ΔP. Engineers strategically place these openings to minimize flow imbalances and losses ΔP.
Remote Heat Exchanger and Secondary Cooling System - Conclusion
To close at the same time the article and the cooling system effectively, it is essential to highlight the significance of secondary cooling systems that use liquid cooling solutions to dissipate thermal energy absorbed via liquid cooling in cold plates.
Secondary cooling systems may also involve additional HX or radiators to regulate the temperature of the cooling liquid further before it circulates back to the cold plates.
In summary, a well-designed cold plate solution is critical in efficiently managing thermal challenges posed by modern electronics, electric vehicle batteries, high-performance computing clusters, and various industrial applications. These solutions play a vital role in safeguarding the longevity and integrity of critical parts, ensuring that they operate within safe temperature limits while maximizing system performance.