Stress Concentration Factor: Minimizing Its Effects in Engineering
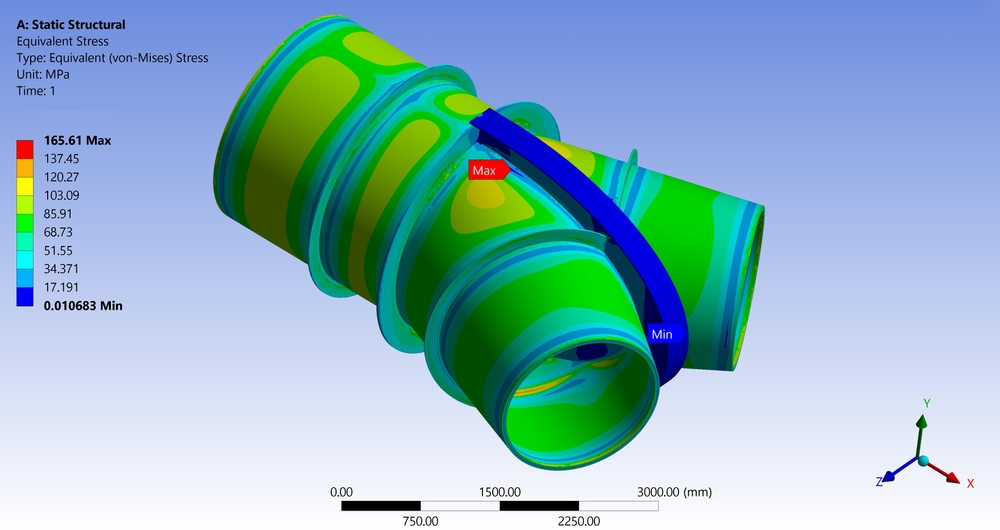
Stress concentration refers to localized regions of elevated stress in a material, often caused by geometric discontinuities, material defects, or external loading. If overlooked, it can lead to premature failure, especially in components subjected to cyclic loading and fatigue. Dramatic examples are turbine blades or engine parts. Thus, an oversight can lead to unexpected failures and safety hazards.
The stress concentration factor is the ratio of maximum stress to nominal stress. A higher factor signals a greater risk of failure in that area, influenced by geometry. Follow us for practical definitions, suggestions, and advanced prediction methods, from FEA (Finite Element Analysis) to 3D Deep Learning.
What is Stress? What is the Stress Concentration Factor?
Stress (sigma, σ) is a fundamental concept in structural analysis. It is the internal resistance a structure develops per unit area when subjected to an external force.
It tells us how much force F is acting on a given cross-section A:
σ = F / A
σ is classified into tensile σₜ (pulling), compressive σ𝚌 (pushing), shear τ (parallel), torsional τₜ (twisting) stress, and combinations like bending (σ_b) (tensile on one side, compressive on the other. Structures often experience multiple σ types simultaneously (e.g., bending + shear in beams)
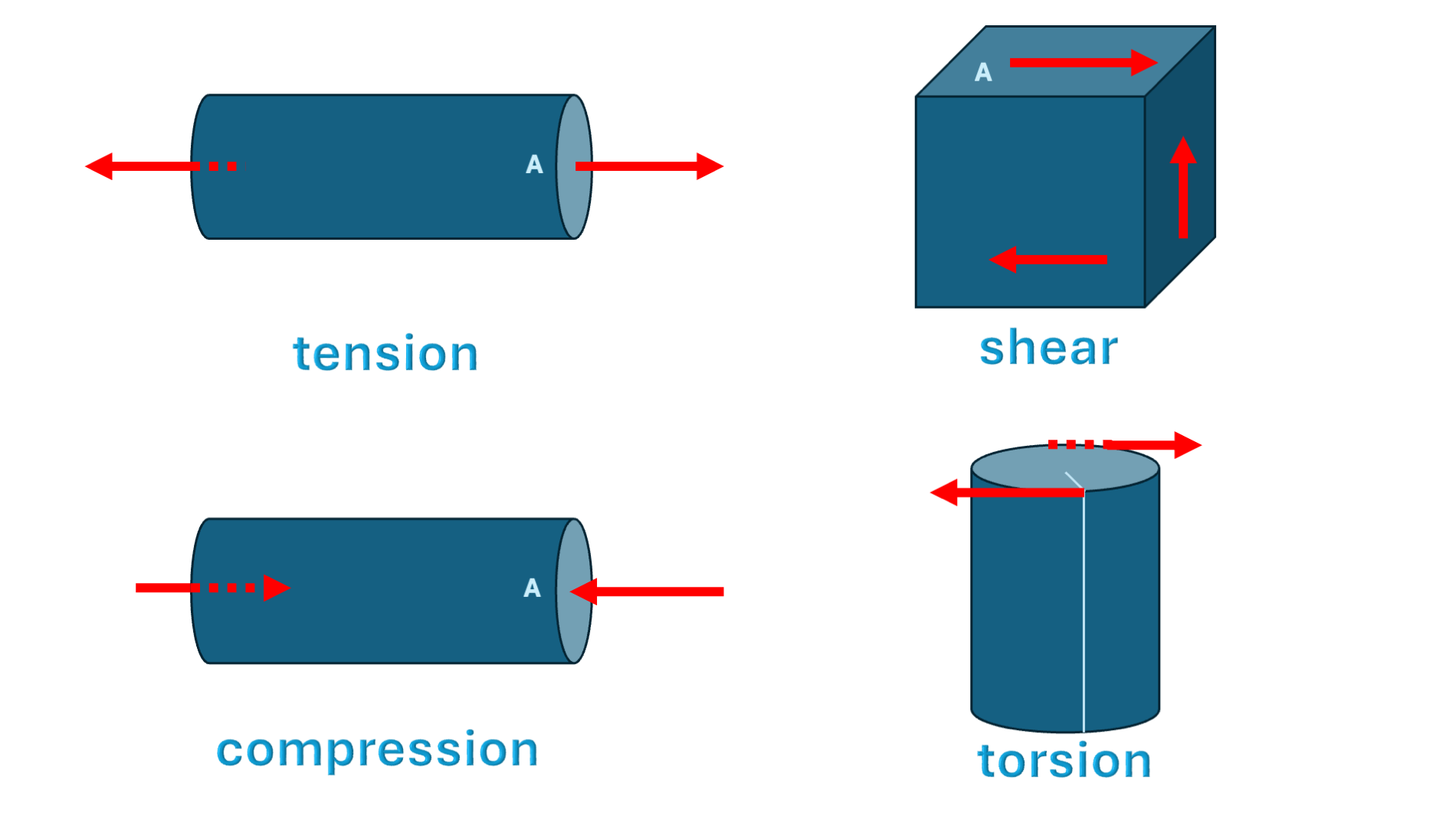
Stress concentration factors quantify how σ is amplified at a point due to local geometric or loading conditions.
The stress concentration factor is:
K = σ_max / σ_nominal
- σ_max = maximum stress
- σ_nominal = applied or nominal σ in the gross cross-section
For a particular nominal stress, the ratio of the highest σ to σ_nominal defines the σ concentration factor. Estimating stress concentration factors requires selecting a reference stress representing the nominal loading condition without geometric irregularities. This reference stress is the baseline for quantifying the amplification effect caused by features like apertures, or abrupt corners.
Engineers refine stress concentration data using experiments or simulations. By comparing computed values with established concentration data, they predict localized peaks with FEA and modify designs to mitigate failure risks.
Typical stress concentration factors (Kₜ) range from 1.5 to 6.5, depending on shape and loading—e.g., 3.0 for a circular aperture in a plate under tension, 2.5–6.5 for a transverse hole in a round bar, and up to 3.8 for bending cases—with engineers refining these values through FEA and experiments to mitigate failure risks.
Effects of Stress Concentration
Stress concentration factors provide insights into potential weaknesses in a structure. Let's review industry examples.
Automotive Industry
In automotive engineering, components experience varying forces, amplifying stress concentrations that reduce lifespan.
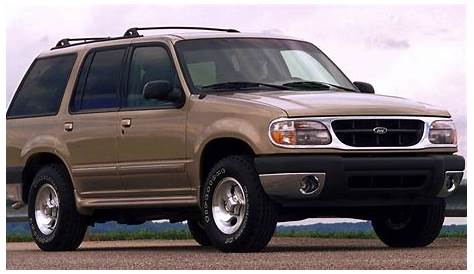
The Ford Explorer/Firestone tire controversy shows how stress concentration affects safety. Tire tread separation stemmed from design flaws that created stress points. These factors led to severe tire failures, prompting improvements in tire design and testing methods.
On this subject, see also "Engineering Analysis Report and Initial Decision Regarding EA00-023: Firestone Wilderness AT Tires" by U.S. Department of Transportation (October 2001).
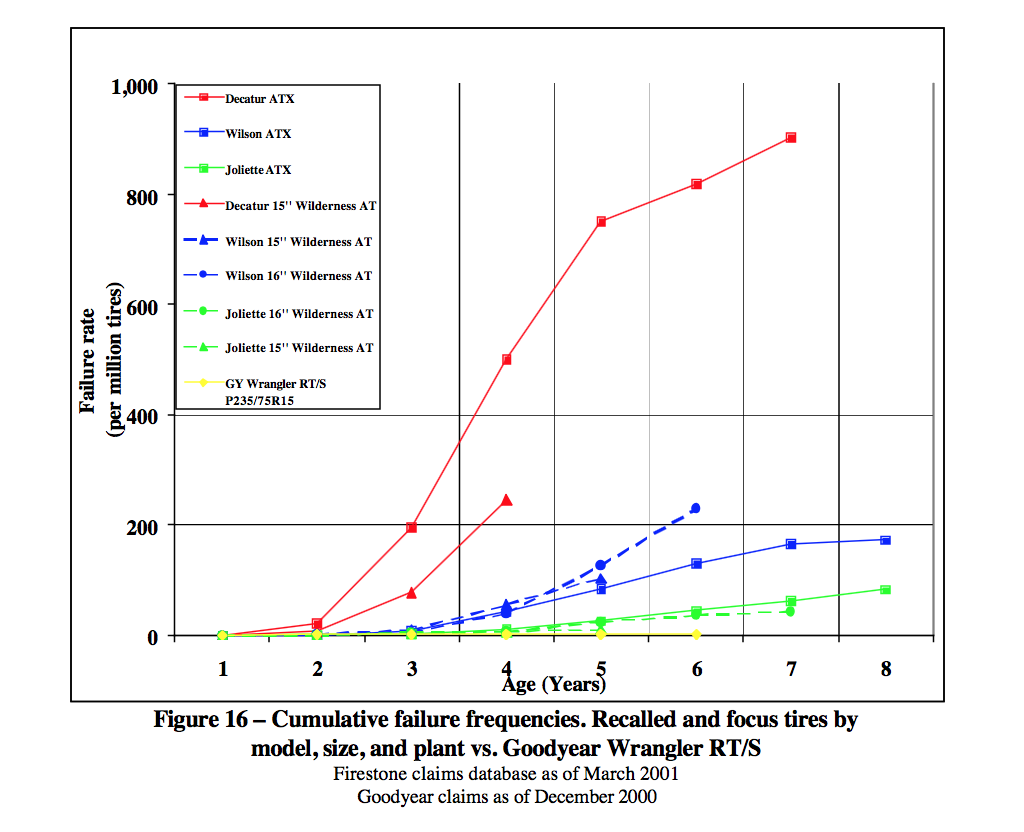
Stress concentrations at tire defects, such as weak spots or belt separations, amplify local stresses, accelerating failure. The high failure rate suggests manufacturing flaws or material inconsistencies, where localized stress exceeds fatigue limits, leading to premature breakdown.
Civil Engineering
In civil engineering, structures endure various environmental conditions and loads. Stress concentrations occur at connection points, changes in cross-section, or material discontinuities, potentially leading to failure under loading from wind and traffic.
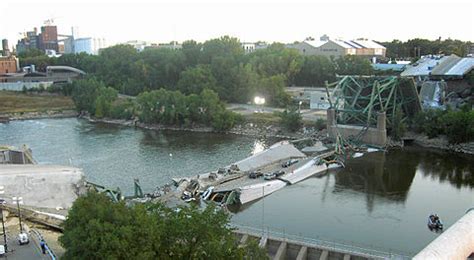
The 2007 I-35W Mississippi River Bridge collapse illustrates the long-term effects of stress concentration in structures. Investigations revealed overly thin gusset plates (see figure), creating stress points at vital connections.
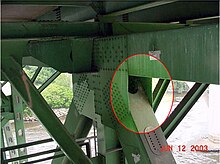
Aerospace
Abrupt geometric changes, like corners, can create streconcentration points that can lead to catastrophic flight failures. For example, window cutouts are specific geometric stress raisers in aircraft fuselages. If not properly reinforced, the maximum stress approaches infinity at abrupt corners, risking structural failure. Fillets and composite materials reduce the highest to nominal stress ratio.
Causes of High Stress Concentration and How to Mitigate It
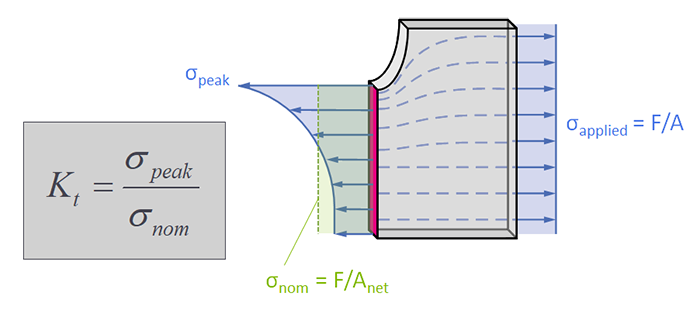
- Sharp corners and notches cause localized stress due to sudden geometry changes, proving an example of a specific geometric stress raiser. The maximum value felt near a crack occurs in the area of lowest radius of curvature.
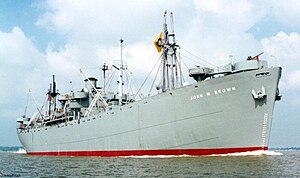
- Holes and cutouts, such as drilled holes or slots, disrupt the stress flow. The Comet Jet crashes in the 1950s illustrate this: window corners acted as stress risers, leading to catastrophic failure.
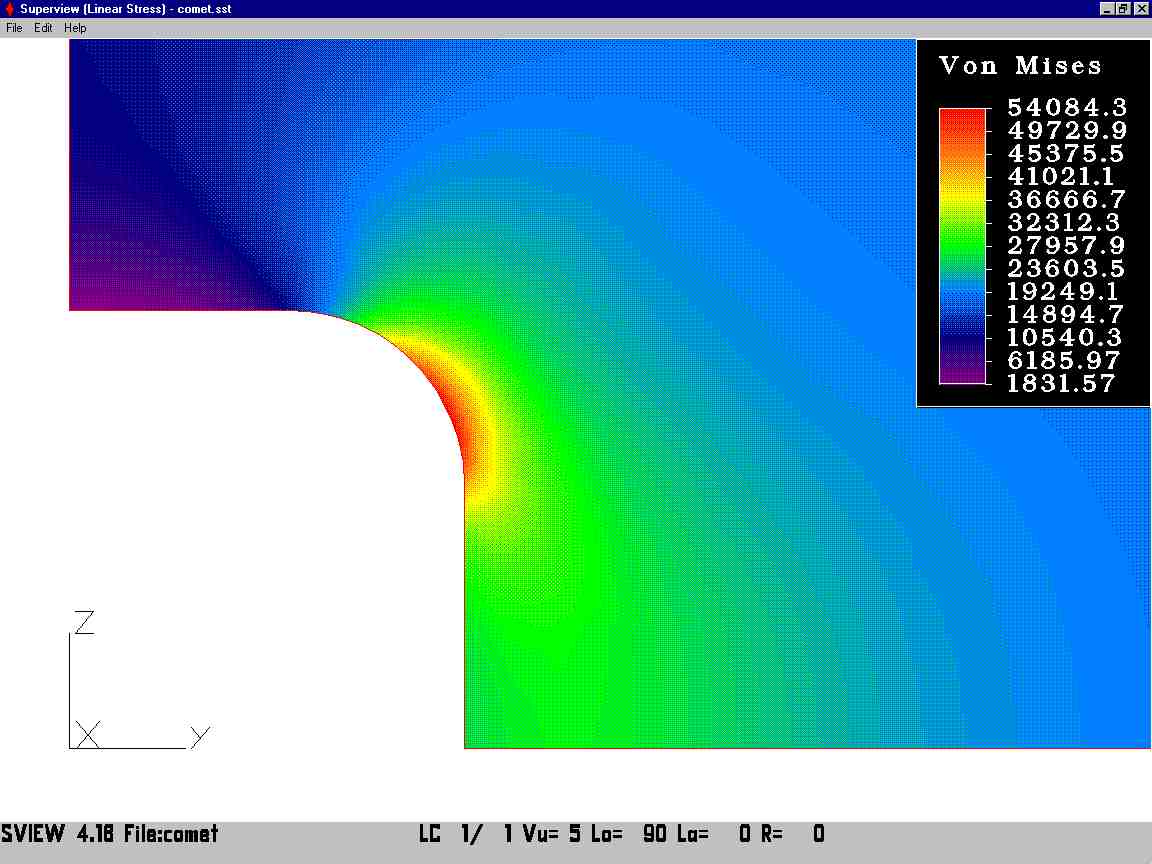
- Material defects, such as inclusions or voids, create weak points. The 1988 Aloha Airlines Flight 243 incident was due to fatigue cracks from rivet holes contributing to fuselage failure.
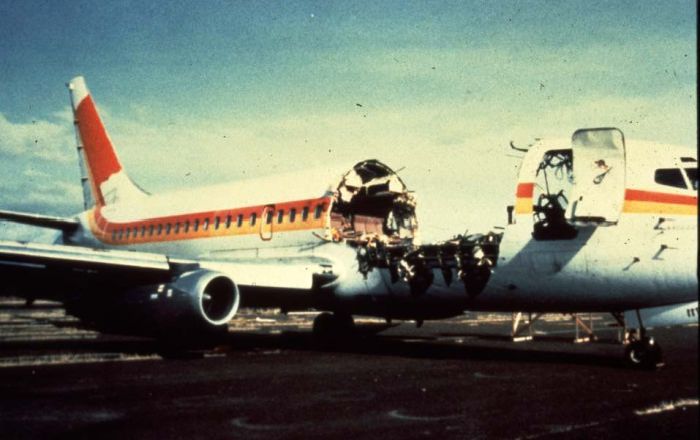
- Abrupt cross-section changes, which are sudden thickness transitions, cause stress spikes.
In summary, in regions with sharp geometric discontinuities, the highest stress can be larger than the applied load’s effect on a uniform section. With notch radius decreasing, the highest stress approaches infinity, making failure more likely.
How to reduce stress concentration?
- Geometric optimization with fillets, smooth transitions, and reinforced materials. Circular shapes for holes instead of diamond-shaped holes reduce the concentration of stress and part material while lowering peak stress.
- Engineers can mitigate the impact of stress concentration by selecting materials with high fracture toughness and fatigue resistance.
- Load redistribution helps achieve more balanced stress distributions
The top diagram (red) in the figure below illustrates a poor design with sharp corners that create severe concentrations, leading to crack initiation and fatigue failure during normal loading. The bottom diagram (green) shows gradual, rounded transitions that eliminate dangerous concentrations. A key principle in mechanical design is avoiding abrupt corners and geometry changes, favoring gradual transitions with fillets to minimize stress concentrations.
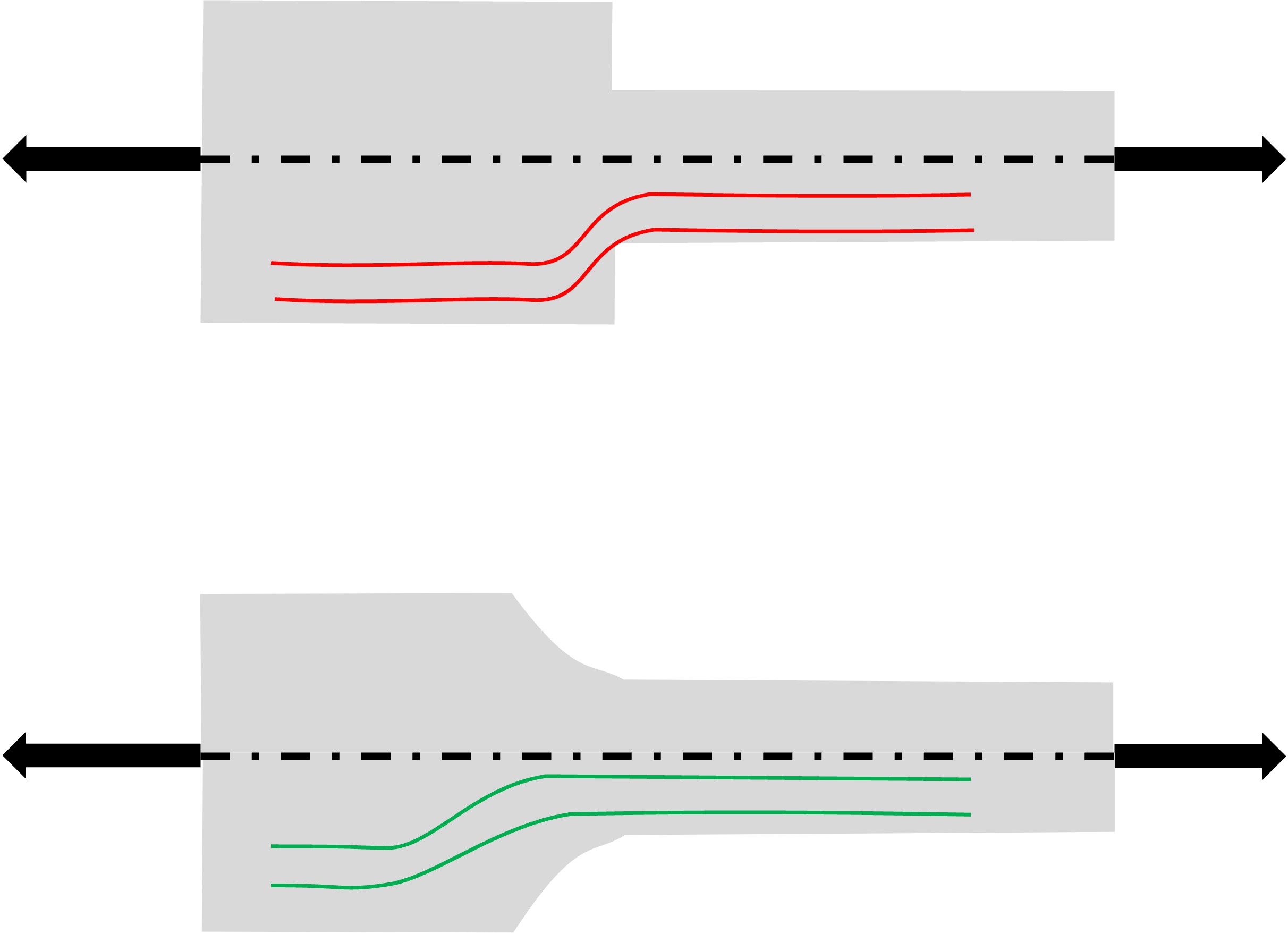
CNC machining techniques can help reduce stress concentrations by designing stress flow points, such as relief notches, and reducing abrupt corners.
Simulation Techniques
Finite Element Analysis (FEA) simulates structural stress distribution and fluid-structure interaction. A key application is estimating stress concentration factors, helping engineers predict localized σ amplification due to geometric features like holes, notches, or sharp edges.
FEA handles complex geometries by breaking them into manageable elements and follows the equilibrium principle, where internal forces balance external loads ∑F_internal = ∑F_external. FEA solves these equations iteratively and visualizes stress distribution, deformation, and displacement in 3D.
Emerging Trends - Conclusion
Deep Learning exploits past FEA analyses and associated CAD geometries to produce prediuctions accessible to all engineers, not just specialists, for addressing stress concentration, such as in the design and optimization of turbo machinery.
Deep Learning indeed shows the potential of AI used in mechanical engineering.
As these systems evolve, they will democratize FEA, making it accessible to smaller organizations that previously lacked the resources for extensive FEA capabilities.
FAQ
What are the experimental methods for stress concentration factors?
Photoelasticity reveals σ patterns in transparent models using polarized light and colored fringes. Strain gauges measure deformation at critical points, allowing calculation of stress concentration factors.
What is the difference between stress concentration factor and stress intensity factor?
The stress concentration factor Kₜ and intensity factors KI/KII/KIII address different aspects. Kₜ quantifies local amplification due to geometric features in components. It is dimensionless and applies to elastic materials. Stress concentration factors help predict where cracks might initiate. The stress intensity factor applies to fracture mechanics and cracked components. It quantifies the severity of σ fields near crack tips and determines whether existing cracks will propagate. Different fracture modes (opening, sliding, tearing) have corresponding factors (KI, KII, KIII).
How do manufacturing processes affect stress concentration in components?
Machining, welding, or casting can introduce imperfections, such as sharp corners, surface roughness, or residual stresses, which act as concentrators.
Can AI fully replace traditional FEA?
AI complements FEA in design departments. It excels at rapidly predicting stress patterns and relies on FEA-generated training data since it lacks the physics-based approach that makes FEA reliable in new situations.
Can you suggest a reference book?
"Peterson’s Stress Concentration Factors" is a reference with empirical data and formulas for calculating Kₜ for various geometric features under tension, bending or torsion. It includes charts and equations helping engineers estimate local stress increases.