EV Battery Cooling: Key Applications and Impact on Performance
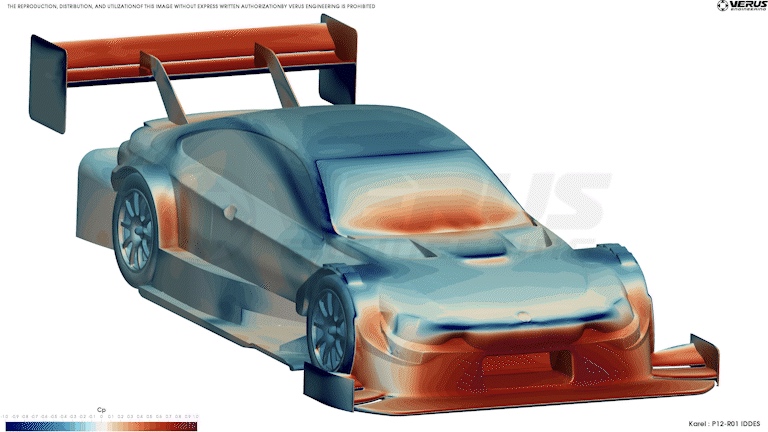
Battery thermal management systems leverage passive air cooling and active heat pump technology to maintain optimal battery temperature, ensuring enhanced performance and longevity. Precise temperature regulation in electric vehicle batteries is essential for sustained functionality and durability of the battery pack and, therefore, the electric motor car. In the article, we will see how the interplay between cooling and heating mechanisms in EV battery cooling underscores the complexity of preserving battery pack integrity while harnessing the full potential of electric vehicles. We will explore the main thermal management methods in which electric vehicle batteries cool, i.e., air and liquid cooling.
We will review the advantages of liquid cooling systems and how AI can assist car manufacturing by providing substantial help to product engineers working on finding efficient heat transfer solutions for battery pack thermal management systems.
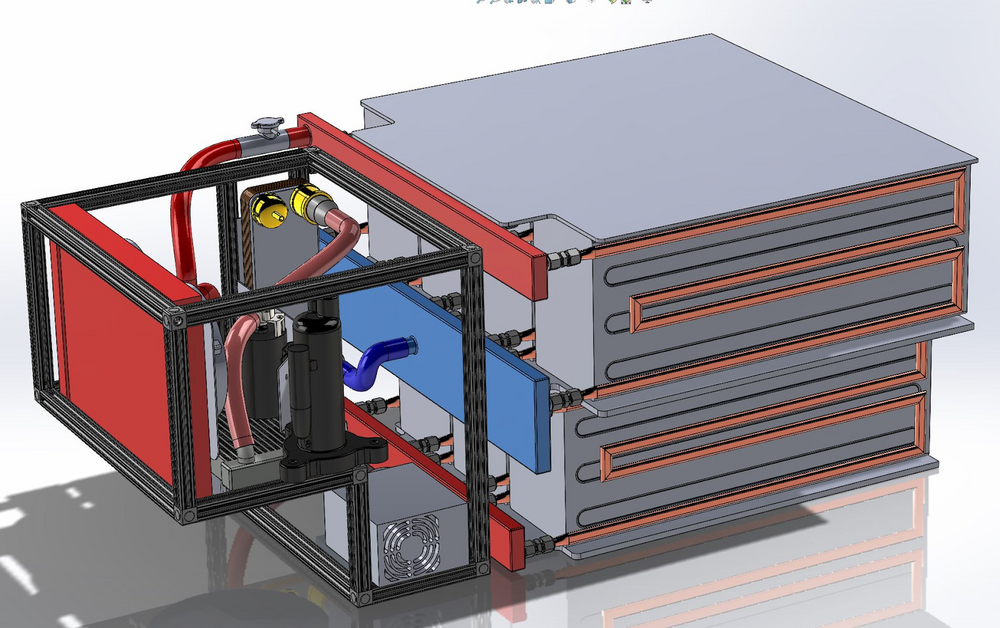
Why EV Battery Cooling? Challenges of Thermal Management
Thermal management systems are crucial for EV battery longevity, as the specific temperature requirements are dictated by battery cell chemistry and physics. Lithium-ion batteries are the most common due to their high energy density and rechargeability.
Let's explore them next and see what challenges to efficient EV battery thermal management poses.
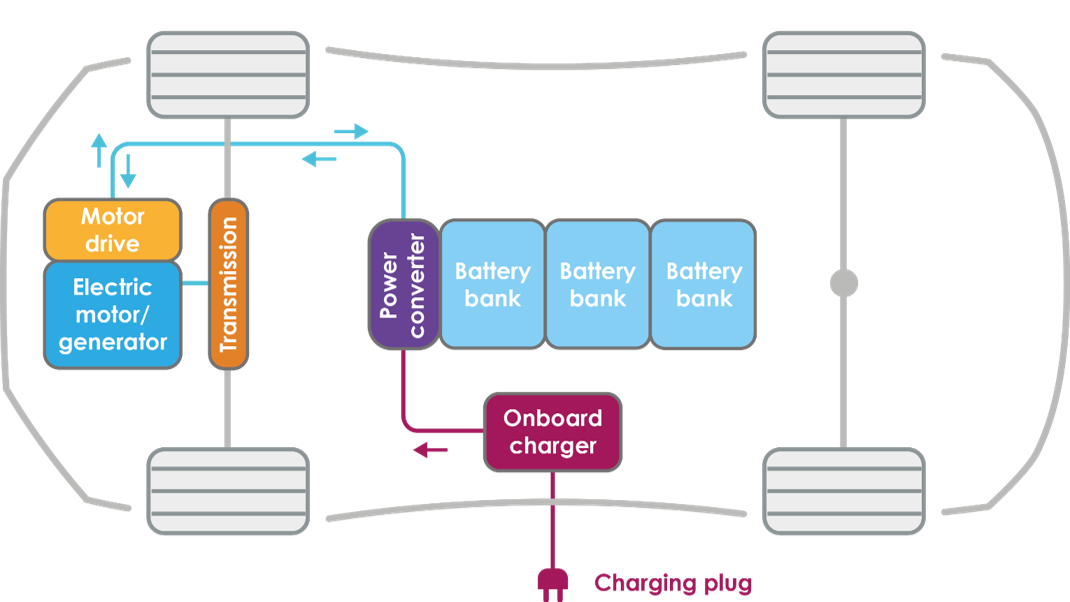
Introduction to Lithium-ion (Li-Ion) Batteries
Li-ion batteries are preferred for electric vehicles (EVs) due to their high energy density and rechargeability. Their performance and lifespan depend on temperature, functioning best between 20 °C and 25 °C. Below this range, ion movement slows, reducing efficiency and power. Cold weather hampers chemical reactions, affecting energy output, acceleration, and range. To mitigate these issues, EVs use thermal management systems to prevent overheating and use optimal temperature management. Cooling systems protect against overheating while heating elements warm batteries in cold conditions to improve performance.
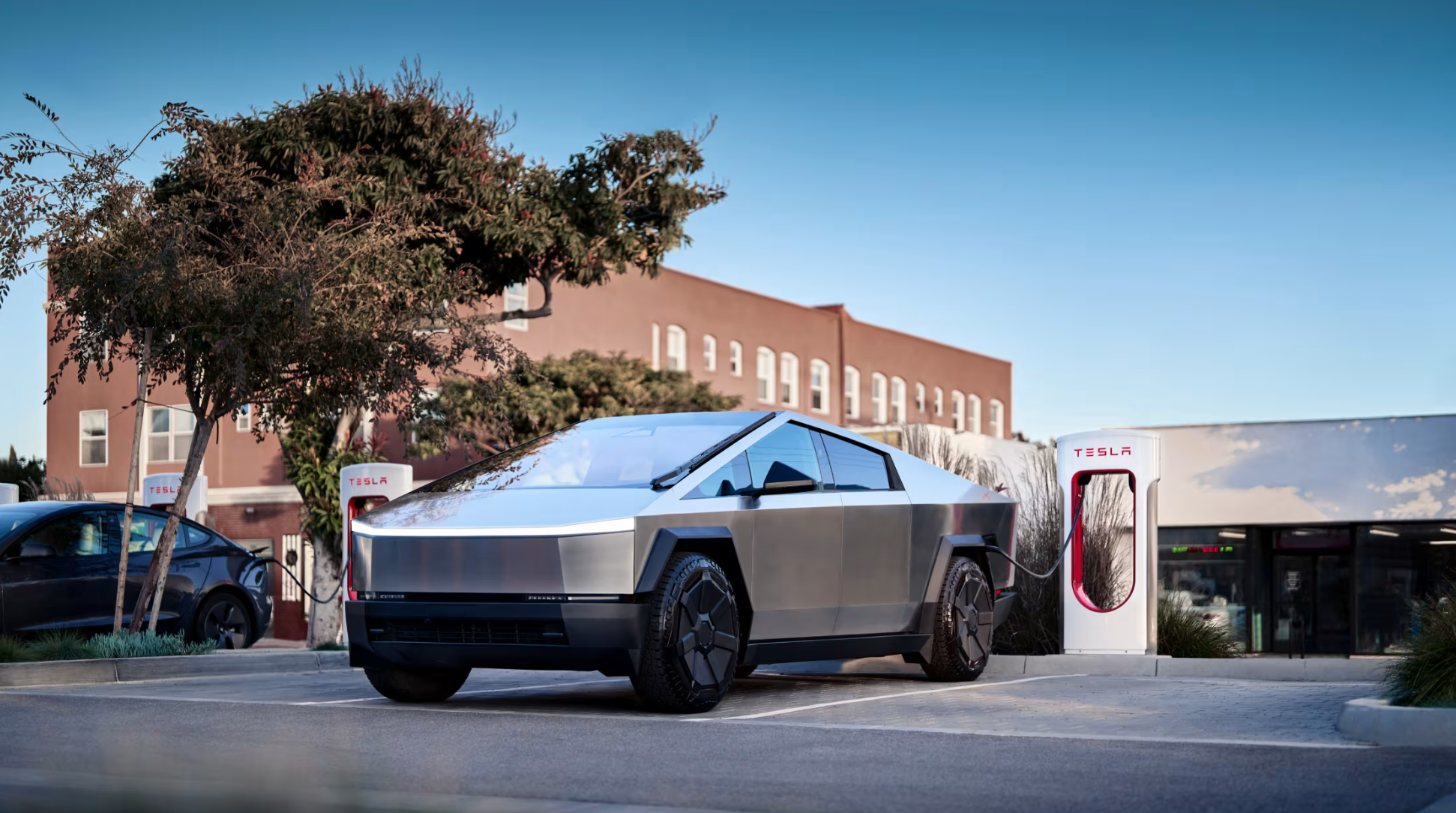
High-Temperature Challenges
High temperatures harm battery performance and lifespan by speeding up electrochemical reactions. This accelerates electrode and electrolyte degradation, reducing capacity and lifespan. Elevated temperatures promote internal dendrite growth, leading to short circuits and safety risks. Thus, controlling battery temperature is crucial for efficiency and stability. Maintaining temperatures between 20°C and 25°C ensures optimal reactions, preserving performance and longevity, which is vital for EVs where reliable power and battery life are expected.
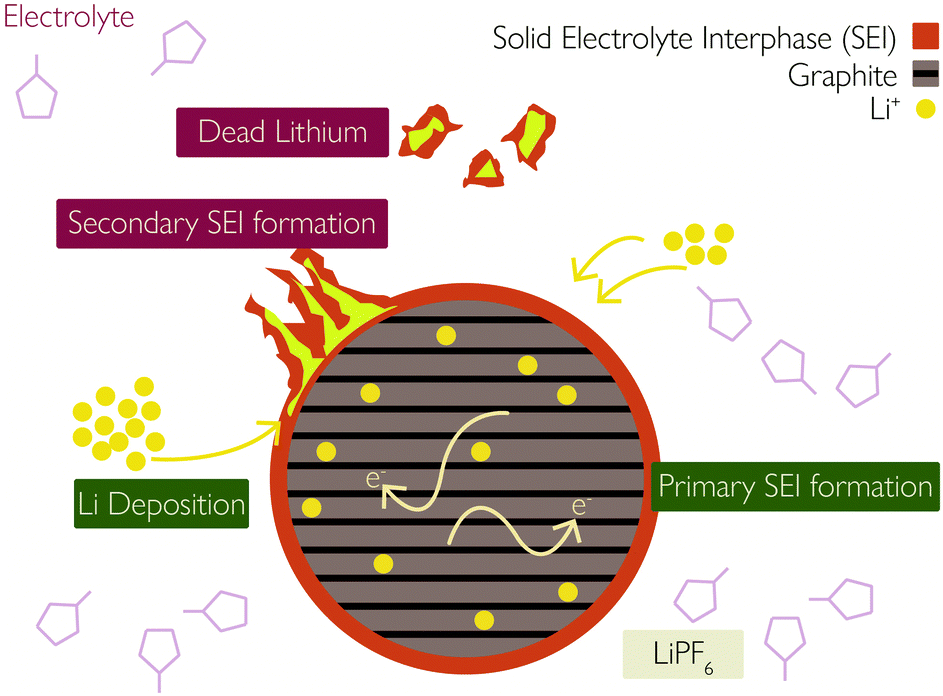
Thermal Runaway
We will now explain the conditions and mechanisms that could lead to EV thermal runaway in lithium-ion batteries.
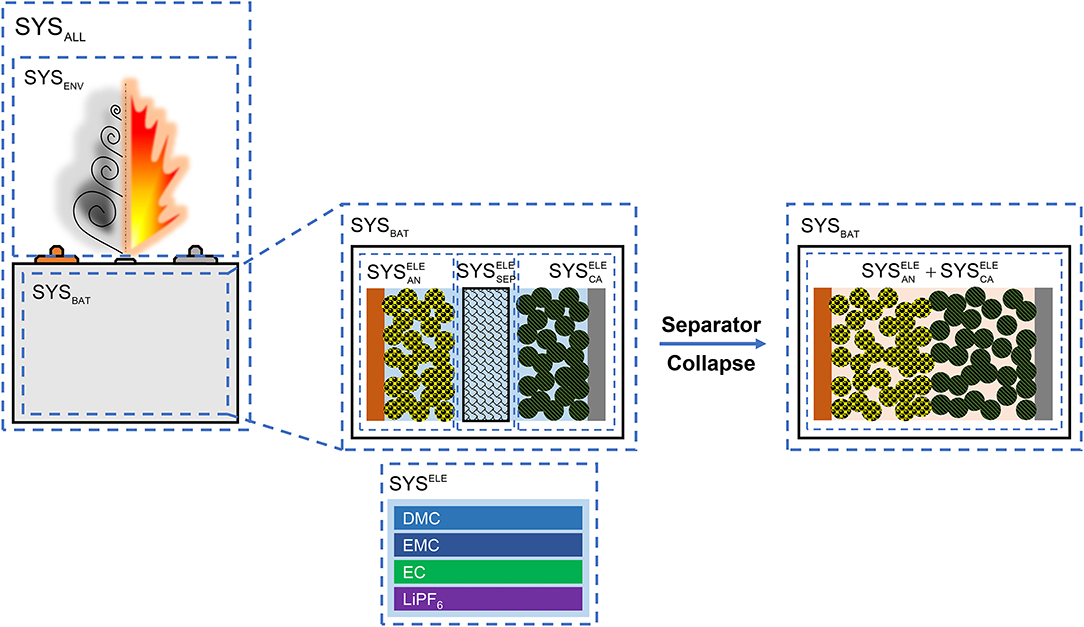
Batteries, particularly Li-Ion, are sensitive to temperature variations, influencing their performance, safety, and longevity. During recharging, the optimal temperature range typically falls between 0°C and 50°C, as chemical reactions within the battery operate efficiently and safely within this interval. Deviating from these limits can hinder ion mobility, reduce charge acceptance, or accelerate side reactions, potentially degrading the battery’s lifespan. During operation, batteries generate heat due to internal resistance and electrochemical reactions. If the heat generated is not effectively dissipated, the temperature can escalate beyond the designed operating range.
Battery Cooling System & Heating System
Facilitating both active and passive cooling methods for batteries becomes imperative during rapid charging processes. This need for direct cooling arises from the heat generated by the high current flowing into the battery during fast charging. Effective battery cooling measures heat dissipation to prevent overheating, safeguarding the charging rate and the battery from potential overheating issues.
Furthermore, EV batteries may require heating mechanisms, primarily when exposed to extremely low temperatures or to enhance performance capabilities. For instance, charging cells below the temperature threshold of 0°C is not feasible for electric cars.
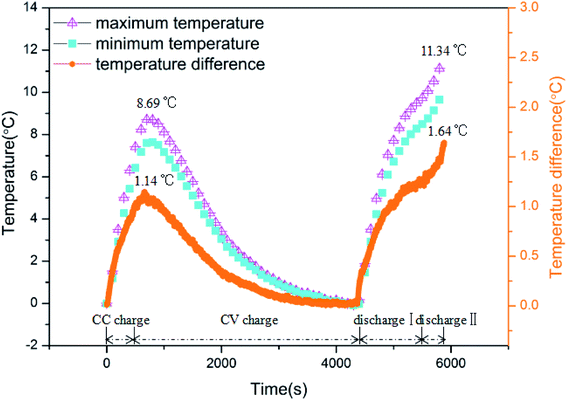
Companies like Tesla employ innovative practices such as battery preheating in certain vehicle models. This approach elevates performance standards, enabling impressive acceleration rates from 0 to 100 km/h in under 2 seconds.
The Importance of EV Battery Cooling Systems
Efficient thermal management is crucial for ensuring EV batteries' performance, safety, and longevity, as it regulates the heat generated during use, charging, and demanding operations. Without proper cooling, uneven thermal distribution can degrade cells, reduce capacity, and shorten battery life. Advanced cooling systems prevent issues like thermal runaway, a dangerous reaction caused by overheating in electric vehicle batteries, and enable fast charging by dissipating heat effectively. In extreme climates, heating and cooling systems ensure reliable performance by cooling overheated cells or preheating cold ones. These systems preserve battery health and functionality, keeping battery temperature within an optimal range.
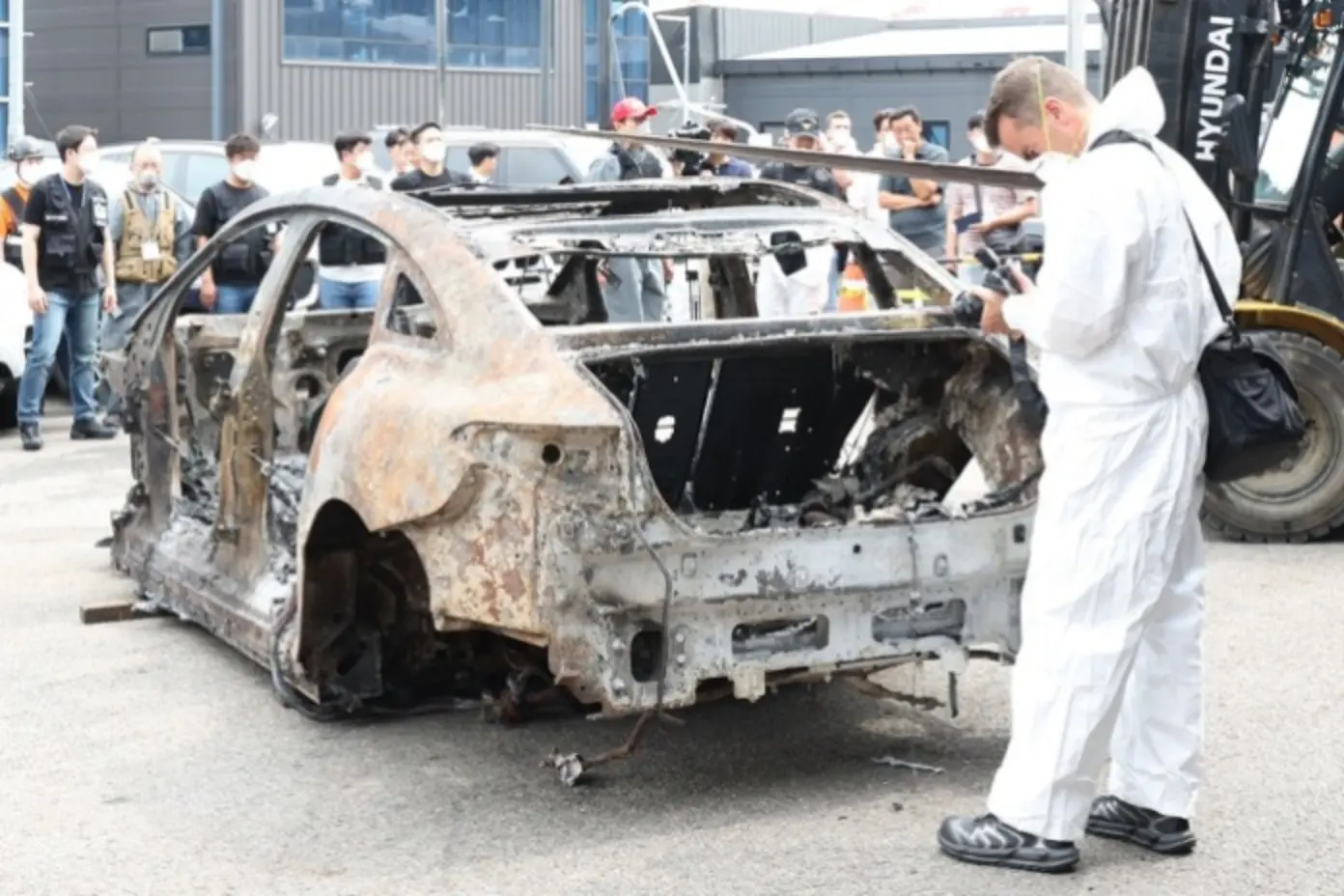
Temperature Control for Longevity
The performance and reliability of electric vehicle (EV) batteries rely heavily on precise thermal management. Batteries operate within a narrow temperature range to avoid degradation, and deviations can accelerate wear or lead to failures. Cooling systems are engineered to regulate heat generated during charging, discharging, and high-demand operations, ensuring that the cells remain stable and efficient over time.
EV batteries naturally generate heat during operation, especially during rapid acceleration, climbing steep inclines, or prolonged high-speed driving. Insufficient cooling causes excessive heat, reducing energy storage and creating uneven thermal distribution, leading to performance imbalances lifespan. Cooling systems prevent this by evenly dispersing heat and maintaining the cells within the optimal temperature window.
Fast Charging Support
Fast charging presents another thermal challenge. The high current flowing into the battery during rapid charging creates substantial heat, which, if left unchecked, can slow the charging process or damage the cells. Advanced temperature management effectively dissipates this heat via liquid cooling systems, phase-change materials, and optimized exchangers.
Thermal Runaway Prevention
The risk of thermal runaway underscores the importance of robust cooling. This chain reaction, triggered by excessive heat, causes a battery's internal responses to spiral out of control, potentially resulting in fire or explosion. Cooling systems safeguard against such events by managing temperatures below critical thresholds. Tesla’s liquid cooling approach exemplifies how precise temperature control reduces the risks associated with overheating.
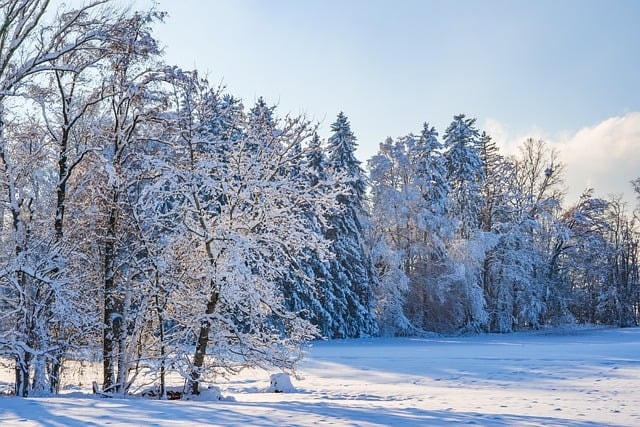
EV Battery Cooling in Extreme Conditions
Thermal management also addresses challenges posed by extreme environments. Batteries can experience reduced efficiency, lower power output, and range loss in cold climates. Integrated heating within the cooling system preconditions the cells, restoring their performance and reliability. Conversely, cooling prevents thermal stress in hot climates, preserving battery health during heavy use.
Cooling systems provide a consistent thermal environment, extending the operational life of batteries and enabling EVs to perform reliably across diverse conditions. Manufacturers continue to innovate, integrating advanced thermal designs to support fast charging, improve safety, and meet the demands of modern electric vehicles.
Types of EV Cooling Systems
Effective thermal management is vital for maintaining the optimal performance and longevity of electric vehicle (EV) batteries. Modern EVs use two primary cooling systems: air cooling and liquid cooling.
Air Cooling
Air cooling systems use forced air to regulate battery temperature by dissipating heat generated during discharging and charging. This method typically involves fans or blowers circulating ambient air over the battery pack to reduce localized temperature peaks. While simple and cost-effective, air cooling is less efficient than liquid cooling, especially under high power demands, as air has lower heat capacity and thermal conductivity. It is often employed in smaller EVs or those with less demanding performance profiles.
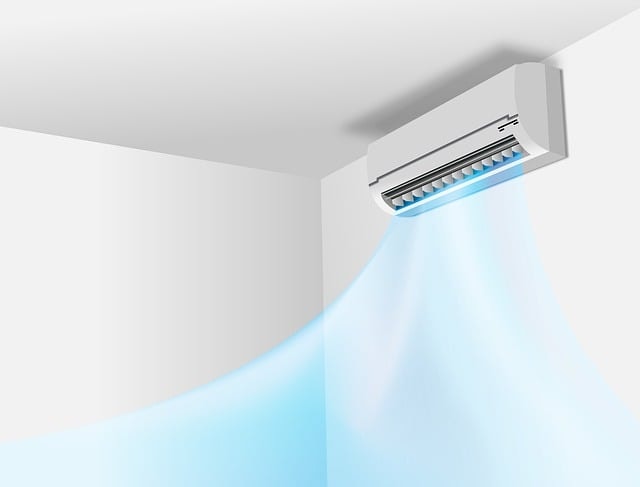
Liquid Cooling
Liquid cooling is a more advanced method that circulates a coolant (typically a water-glycol mixture) through channels integrated into or around the battery pack. This system offers superior heat transfer due to liquids' higher specific heat capacity than air. The coolant absorbs excess heat from the battery and carries it to a heat exchanger or radiator, dissipating it. Liquid cooling is favored in high-performance EVs and larger battery packs, where maintaining precise temperature control is critical for fast charging, long-range driving, and overall battery health.
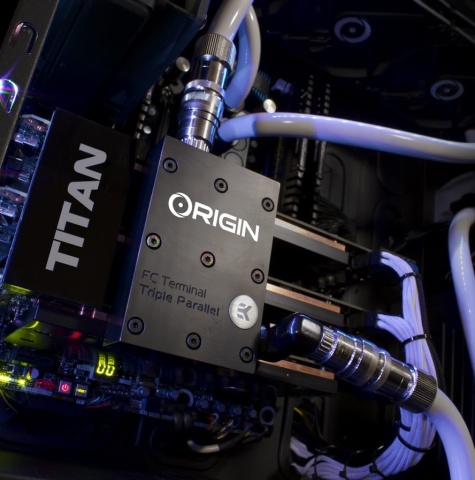
Emerging Technologies
Let us briefly review innovative cooling methods, such as enhancing battery performance with immersion cooling.
Immersion cooling can be categorized into single-phase and two-phase systems. In single-phase immersion cooling, batteries are submerged in dielectric fluids such as HFE or mineral oils, enabling convective heat dissipation with heat transfer rates enhanced 1,000 times compared to air cooling. In contrast, two-phase systems utilize latent heat, where the dielectric fluid boils to absorb heat and subsequently condenses, achieving heat transfer efficiency up to 10,000 times greater than air cooling. However, challenges regarding fluid compatibility and effective system sealing persist.
Hybrid cooling merges immersion techniques with air cooling or incorporates liquid alongside Phase Change Materials (PCMs). This approach aims to maintain uniform temperatures, minimize gradients, and utilize passive and active cooling mechanisms. It necessitates sophisticated control systems for mode switching.
Simulation for Optimal Design of Battery Cooling Systems
Engineers use Computational Fluid Dynamics (CFD) to enhance battery cooling systems with virtual design modifications through simulations, enabling adjustments to cooling channels, flow rates, and fin placements for thermal performance evaluation. After iterations, engineers finalize designs that maintain stable battery temperatures, forming the foundation for electric vehicle (EV) cooling systems. Manufacturers rely on CFD to ensure efficient battery operation, prevent overheating, and extend battery life.
CFD advantages include: 1. Visualizing Temperature: It reveals temperature and fluid mechanics like an X-ray. 2. Testing Designs: Engineers explore options digitally to choose the best before prototyping. 3. Issue Prevention: CFD identifies problems, enabling fixes for overheating. 4. Efficiency: It accelerates design processes by quickly finding practical solutions.
3D Deep Learning enables quick decision-making in cooling systems, processes data efficiently, and enhances sensor information.
It also helps designers verify designs independently using simulation emulators, replicating real-time battery crash tests for the design of innovative lightweight components.
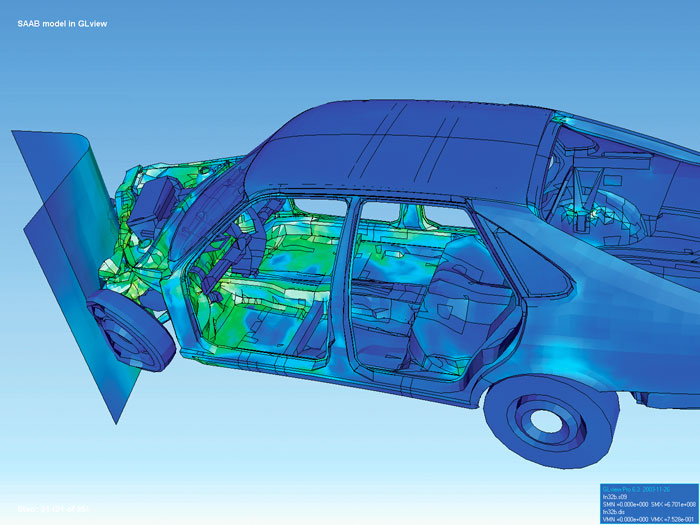
Thus, Deep Learning approaches are beneficial to speed up the iterative design process.
Cooling Systems and Fast Charging
Fast charging induces substantial heat due to high current densities and internal resistive losses within the battery. Advanced thermal management employs liquid cooling, circulating thermal fluids through microchannels integrated into battery packs, effectively extracting heat. Coupled with phase-change materials (PCMs) or vapor-compression cycles, these systems buffer thermal peaks and maintain cell temperatures within optimal thresholds. Such precision minimizes thermal degradation, ensuring charge rate consistency and preserving electrolyte stability during high-power operations.
Cooling systems optimize thermal equilibrium across battery cells, enhancing power output and extending driving range under variable loads. Uniform temperature control mitigates thermal cycling and associated material fatigue, prolonging cell lifespan. Cooling infrastructure minimizes downtime and maintenance costs by reducing the risks of thermal runaway and heat-induced failures. Advanced designs integrating real-time diagnostics and predictive algorithms further enhance system reliability, addressing performance degradation preemptively and reducing the total cost of ownership..
Future Challenges and Innovations in Cooling Systems
The following innovations will improve cooling systems' efficiency, lower environmental impact, and mofd reliability, which are crucial for advancing next-generation electric mobility.
Sustainability Challenges
Traditional cooling systems use glycol or synthetic refrigerants with a high global warming potential, which raises environmental concerns: nontoxic, biodegradable refrigerants and water-based fluids lower ecological impact. Efficient systems reduce energy use by auxiliary coolers, boosting vehicle range and efficiency. Innovations like microchannel heat exchangers and low-pressure-drop circuits improve cooling and reduce energy consumption.
AI-Driven Systems
AI-driven cooling technologies use machine learning to offer adaptive thermal management. These systems analyze real-time data from temperature sensors and battery management systems to forecast thermal loads during rapid accelerations or fast charging. Predictive algorithms activate specific cooling strategies, adjust coolant flow, and optimize thermal gradients across battery cells, reducing hotspots and thermal stresses. This method enhances thermal efficiency and extends the lifecycle of cooling components by minimizing wear.
Advanced Materials
Emerging materials like phase-change materials (PCMs) and thermally conductive composites are revolutionizing battery cooling. PCMs absorb latent heat during phase transitions, storing thermal energy while maintaining isothermal conditions. Encapsulated in polymer matrices, they work with active cooling systems to smooth transient thermal spikes. High thermal conductivity fillers such as graphene, carbon nanotubes, or boron nitride nanosheets enhance heat transfer in thermal interface materials (TIMs). Advanced coatings for heat exchangers use nano-engineered surfaces to reduce fouling and improve long-term cooling reliability.
Conclusion
In conclusion, the article emphasizes the role of thermal management in EVs and details the advantages and complexities of air versus liquid cooling systems. It addresses the challenges of maintaining battery integrity, preventing thermal runaway, and supporting fast charging. Innovations such as immersion and hybrid cooling, AI-driven optimizations and advanced materials like PCMs, are highlighted as key to future improvements in battery performance, safety, and environmental impact.
FAQ
Which EVs have air-cooled batteries?
Nissan LEAF and Volkswagen e-Golf are examples of EVs with air-cooled battery systems. These systems rely on passive or active airflow to regulate temperature, though they may be less effective than liquid cooling in extreme climates.
Are Tesla batteries air-cooled?
No. Tesla batteries use liquid cooling systems that circulate coolant through channels to maintain optimal temperatures. The Tesla approach provides more effective thermal management, especially during fast charging or extreme operating conditions.
Can you damage an electric car battery?
Unfortunately, yes! Overcharging, deep discharging, extreme temperatures, or physical damage can degrade battery capacity and lifespan. Proper charging practices, temperature regulation, and avoiding impacts help mitigate these risks.
Can EV batteries operate in cold climates?
Yes, they can! EV batteries can operate in cold climates even if with reduced efficiency. Modern EVs incorporate battery heating systems to maintain performance by preheating cells during charging or driving in low temperatures.
How do EV cooling systems impact maintenance and reliability?
Advanced cooling systems reduce thermal stress, extend battery life, and prevent overheating or runaway risks. While adding complexity, they enhance reliability and reduce long-term maintenance costs by preserving battery health.
Further Reading
"Lithium-ion battery degradation: what you need to know" DOI: 10.1039/D1CP00359C (Perspective) Phys. Chem. Chem. Phys., 2021, 23, 8200-8221
"Materials for lithium-ion battery safety" DOI: 10.1126/sciadv.aas9820, Science Advances, 22 Jun 2018, Vol 4, Issue 6