Optimizing Aerospace Product Development: Key Trends
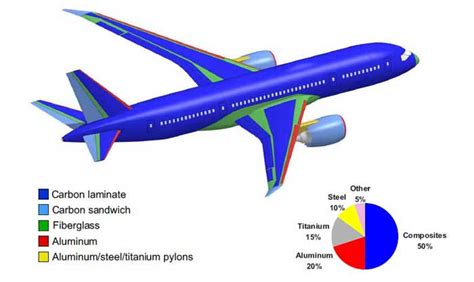
Every industry needs to stay competitive in a rapidly evolving global market, and the aerospace industry is no exception. Indeed, the development process of aerospace products has to adapt itself to the increasing demands for efficiency, sustainability, and cost-effectiveness.
As an example, the shift to lightweight materials with advanced composites like carbon fiber, which are both lighter and stronger than traditional materials like aluminum, has improved fuel efficiency.
On top of lighter material, in both commercial space and defense applications, market demands are pushing for advanced propulsion and enhanced safety: an example is combining electric motors with conventional jet engines to improve fuel efficiency and reduce environmental impact.
Thus, designs have become more complex and agile, and the role of systems engineering increases, since designers have to manage all the interdependencies between the various subsystems composing an aircraft.
Aerospace product development is not, however, up to single solitary "geniuses". Rather it is highly multidisciplinary, involving for instance teams in design, propulsion experts, aerodynamicists, and materials experts.
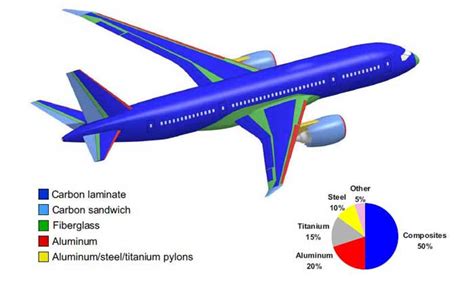
Multidisciplinary-oriented teams in aerospace product development are essential to integrating the subsystems we mentioned, i.e. all the numerous components and technologies involved in modern aircraft.
However, the path is challenging. Current challenges in this field include reducing time and costs while ensuring performance and safety. Traditional methods like computer-aided design (CAD) are no longer sufficient on their own to meet these performance goals. There is a growing need to enhance the process of development through advanced digital tools and techniques.
One area of opportunity is the incorporation of artificial intelligence (AI) into the design stage. AI can optimize product development by improving decision-making, automating routine tasks, and predicting potential design flaws before they become critical issues. This helps streamline the process of development, making it more efficient while maintaining the high standards of safety and reliability expected in the industry. Additionally, AI in aerospace industry enhances collaboration across multidisciplinary-oriented teams by offering insights that can be applied across different aspects of design.
Ultimately, innovation in the industry—driven by AI and an improved process—will be key to addressing current challenges and meeting future performance requirements from markets.
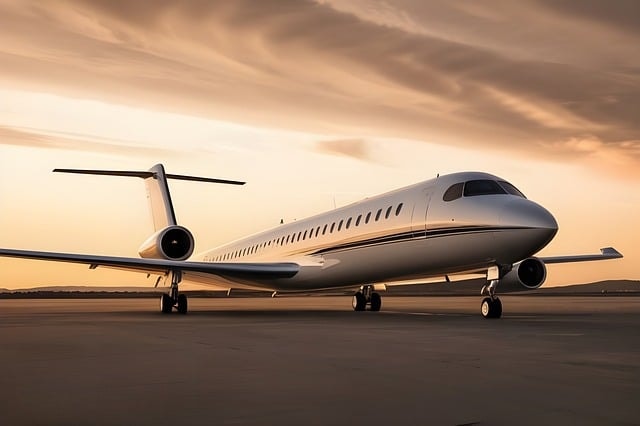
What Is Aerospace Product Development?
The aerospace industry operates within a highly regulated environment where every step in the process of development must adhere to strict guidelines and quality standards. Design is the foundation of product development. Design engineers use tools like CAD to create detailed models of components and systems. These designs are crafted with a specific focus on enhancing performance and safety and reducing costs, ensuring they meet the demands of modern technologies from the market.
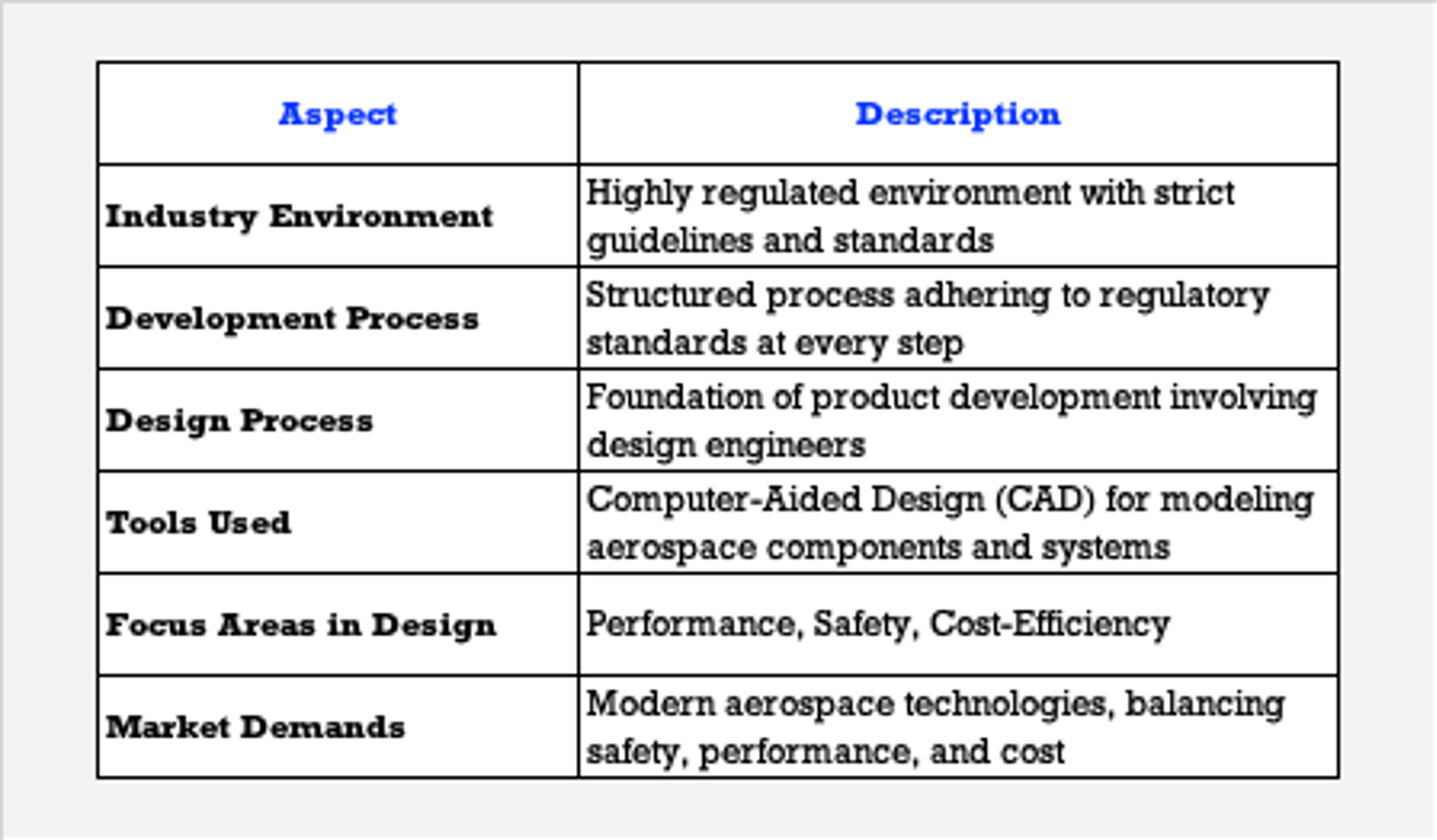
Design and Engineering Phase
The initial phase involves conceptualizing the product, whether a new propulsion system, an aircraft component, or an integrated system for space applications.
The Design & Engineering stage relies heavily on the expertise of teams who specialize in different areas such as mechanical engineering, electrical engineering, or software engineering, including a team of experts in data science. Engineers collaborate to develop both individual components and entire systems.
Advanced simulation tools and high-end hardware resources such as HPC (high-performance computing) private clusters or cloud resources such as Microsoft Azure are often used to model and test designs virtually before any physical development takes place.
This collaboration helps the integration of simulation in the design process to deliver results at unprecedented levels of response time and details of prediction of 3D structures like vortices to increase aerodynamic performance in an agile way not requiring expensive and tedious physical testing and prototyping cycles.
Simulation helps optimize the design processes and reduces development costs. As of today, any major company has this capability in-house, in collaboration with vendors and universities.
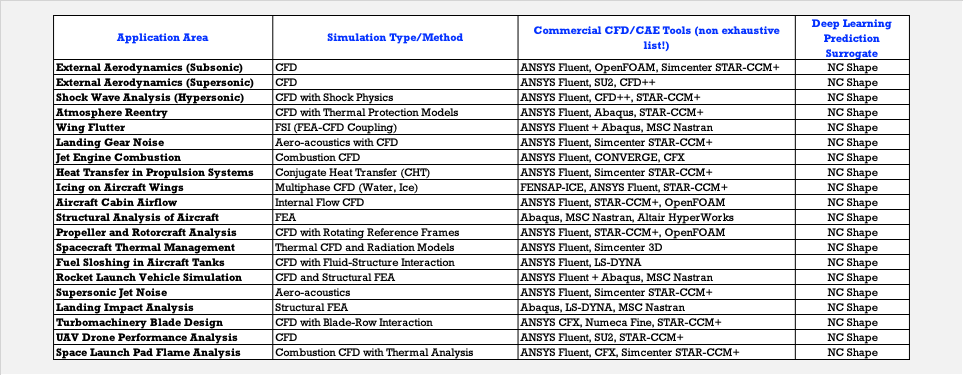
Process Development and Engineering Phase
Systems engineering is critical in product development as it focuses on integrating various subsystems into a coherent whole. In aircraft development, subsystems such as propulsion, avionics, and structural integrity must work together seamlessly.
A key aspect of this integration is the manufacturing process, which ensures that the technologies and materials chosen are not only optimized for performance but also cost-efficient and scalable for large-scale production. Advanced manufacturing methods, such as additive manufacturing (3D printing) and automated assembly, play a crucial role in enabling the production of complex components while reducing waste and production time, ultimately ensuring that designs can be realized effectively and at scale.
Compliance with Regulatory Standards
Aerospace products must adhere to rigorous standards - probably the most stringent in the world with nuclear and pharma! These standards ensure that the development process aligns with protocols, operational efficiency, and (last but not least) environmental considerations. Meeting these standards is not "an option", but a legal requirement. Failure to comply can result in penalties or, worse, real product failures with catastrophic consequences for equipment, structures, staff, passengers, or even unaware citizens.
Regulatory standards apply to all types of products, from military aircraft to spacecraft and civil aircraft, and cover every process, spanning from material selection practices to testing protocols.
Multidisciplinary Collaboration
Aerospace product development requires multidisciplinary teams that work together across different areas of expertise, such as mechanical, electrical, and software engineering. These teams integrate their knowledge to ensure designs meet the complex requirements of modern systems as the above quoted regulatory constraints, or quality indices. Effective collaboration is vital to managing the complexities of products and systems, as each component often relies on another to function correctly.
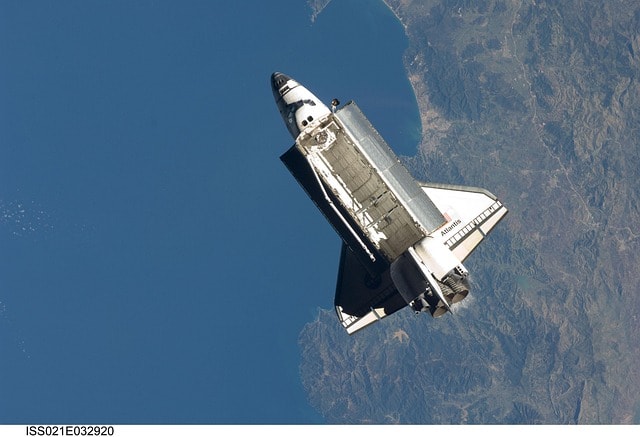
Testing and Validation Phase
Once the initial design phases are complete, thorough testing and validation are required. This is a critical stage to ensure the product meets all standards. Both physical and simulated tests are used to evaluate the product under different operational conditions.
High-end testing practices in the industry often include stress tests, wind tunnel testing for aircraft, and simulations for space.
The Agile Approach
Agile refers to a flexible and iterative approach that allows teams to rapidly adapt to changing requirements and challenges. Unlike traditional waterfall models, Agile promotes continuous collaboration, shorter development cycles, and frequent testing to incorporate feedback at every stage. This approach is particularly valuable when ongoing adjustments are needed. Agile methods, such as Scrum or Kanban, enable faster innovation, reduced risk, and better alignment across multidisciplinary teams, helping manage the intricacies of integrating new technologies, new material types, and innovative manufacturing processes.
Through iterative cycles and frequent testing, the Agile approach allows teams to identify cases of failure such as potential design flaws, preventing them from escalating into larger and more expensive failures later.
Best Practices for Optimization
Traditional processes in design often require time-consuming simulations, but AI can predict outcomes more efficiently by learning from previous data. This allows teams to explore multiple design alternatives in less time, optimizing critical factors like aerodynamics, weight, and material strength. AI-driven simulations are especially useful to enable real-time feedback during the design process, helping teams quickly identify and address issues, leading to faster decision-making and reduced development cycles. A 3D Deep Learning AI platform can provide a full "alternative" for designers to the overwhelmingly advanced CAE software described below.
The Role of Advanced 3D Modeling Software
Advanced software such as Computational Fluid Dynamics (CFD) and Finite Element Analysis (FEA) is essential for evaluating complex 3D physical behaviors ranging from vibration and fatigue to heat and aerodynamic lift. This numerical software models the behavior and performance of components under various conditions, from stress and vibration to airflow and heat transfer.
While generating valuable insights, CAE software also generates huge amounts of data that can be "recycled" later on by AI.
CFD
Computational Fluid Dynamics (CFD) is essential for predicting flight performance by simulating how air interacts with surfaces, allowing experts to optimize designs for lift, drag, and fuel efficiency. Through iterative CFD simulations, designers can assess aerodynamic behavior under various flight conditions, ensuring safer and more efficient flight operations.
Another typical application is space re-entry. Since the conditions in space and atmosphere are different, CFD simulations help predict the flow patterns and thermal loads that spacecraft experience during re-entry, modeling the interactions between the spacecraft and the atmospheric gases.
AI-Driven Design Optimization
AI algorithms can analyze complex design variables embedded in CAD and quickly generate optimized solutions. In CAD, AI-driven software assists engineers by suggesting design improvements, automating repetitive tasks, and exploring more efficient shapes and configurations. AI brings advanced processes from Finite Element Analysis (FEA) and Computational Fluid Dynamics (CFD) to CAD designers, enabling faster and more accurate assessments of product performance under various conditions, for instance, a flight envelope based on external aerodynamics simulation. This AI learning process from FEA and CFD helps designers create innovative products
Sustainability in Aerospace
Sustainability is becoming increasingly important, driven by market demands for more efficient and environmentally friendly technologies. The industry faces challenges such as reducing emissions, optimizing fuel consumption, and minimizing waste in the product development process. Aerospace companies are focusing on developing sustainable propulsion systems for both commercial aircraft and defense aircraft, incorporating advanced and lighter components to improve efficiency.
AI is playing a crucial role in advancing sustainability by optimizing the process of design, predicting system behaviors, and enhancing operational efficiency.
Early implementation of AI in product development facilitates smarter use of resources, reducing both cost and environmental impact. For instance, AI software is used in CAD to refine aircraft designs for improved aerodynamics and lower fuel consumption in projects.
Moreover, multidisciplinary project teams in aerospace are using AI to manage complex systems and data, optimizing processes: this includes high-level simulations to assess environmental impacts throughout the product lifecycle.
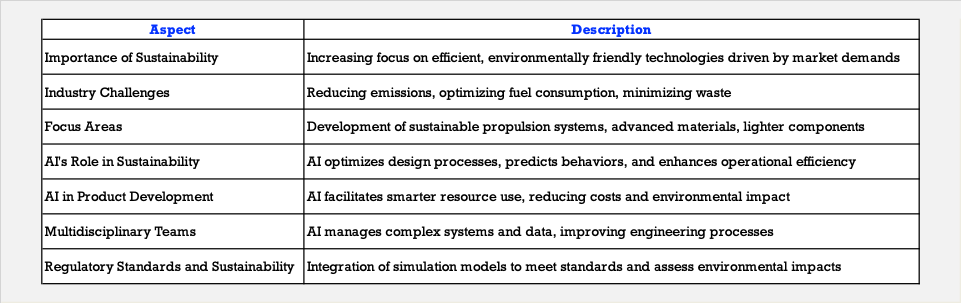
Conclusion
Aerospace product development is adapting to increasing demands for optimization. Key trends include the shift to lightweight composites, like carbon fiber, which are both stronger and lighter than traditional metals such as aluminum, improving fuel efficiency. Advanced hybrid-electric propulsion systems are also being developed to reduce environmental impact.
Advanced high-fidelity software like CFD and FEA are integrated into AI-enhanced platforms to optimize system performance and reduce costs. This combination of AI and CFD or FEA helps companies and their technology suppliers meet strict standards while pushing innovation in sustainability and efficiency.
The process has become highly multidisciplinary, involving experts in design, propulsion, aerodynamics, and material science. Companies that operate with new innovative technologies such as AI-driven simulations are at the forefront of the new approach of accelerating design iterations and improving decision-making, allowing engineers to explore multiple design alternatives more quickly with the highest levels of quality, with cost and risk reduction always present as objectives.